Preparation method of low-silicon high-magnesium iron ore pellets
A technology of high-magnesium pellets and iron ore pellets, applied in the field of metallurgy, can solve the problems of wide reflow temperature range of pellets, high price of nodular iron fine powder, high-silicon and low-magnesium pellets are not suitable for large-scale smelting, and reduce waste , Excellent metallurgical performance, and the effect of improving production efficiency
- Summary
- Abstract
- Description
- Claims
- Application Information
AI Technical Summary
Problems solved by technology
Method used
Image
Examples
Embodiment 1
[0037] 1) Magnesium-containing low-silicon iron concentrate powder (in terms of mass fraction, Si: 2.7%, magnesium: 1.6%) is finely ground to obtain iron concentrate powder, and the -200 mesh particle size of iron concentrate powder is 65%;
[0038] Step 1) The iron ore concentrate powder is magnesium-containing low-silicon iron ore concentrate powder, in terms of mass fraction, Si: 0.5%-4.5%, magnesium: 0.5%-3.8%. 2) Mix iron concentrate powder and binder bentonite into a mixture, the weight ratio is: iron concentrate powder 97%, binder 3%;
[0039] 3) The mixture is subjected to high-pressure roller milling, drying to a moisture content of 6%, and then mixed with a powerful mixer;
[0040] 4) The mixture is made into pellets by adding water to the disc pelletizer, and the amount of water added is 8% of the total amount of materials. After passing through the vibrating screen, the qualified raw pellets with a particle size of 9-15mm are sieved;
[0041] 5) Qualified green ba...
Embodiment 2
[0045] 1) Magnesium-containing low-silicon iron concentrate powder (in terms of mass fraction, Si: 2.9%, magnesium: 1.9%) is finely ground to obtain iron concentrate powder, and the -200 mesh particle size of the iron concentrate powder is 68%;
[0046] 2) The iron concentrate powder and composite binder are formulated into a mixture at a ratio of 99.5:0.5, and the weight ratio is: 99.5% iron concentrate powder and 0.5% binder;
[0047] 3) The mixture is subjected to high-pressure roller milling, drying to a moisture content of 8%, and then mixed with a powerful mixer;
[0048] 4) The mixture is made into pellets by adding water to the disc pelletizer, and the amount of water added is 9% of the total amount of materials. After passing through a vibrating screen, qualified raw pellets with a particle size of 9-15mm are screened out;
[0049] 5) Qualified raw balls are transported to the grate machine for drying and preheating. The preheating temperature is controlled at 1100°C,...
Embodiment 3
[0053] 1) Magnesium-containing low-silicon iron ore concentrate powder (by mass fraction, Si: 0.5%, magnesium: 3.8%) is mixed with high-silicon iron ore concentrate powder (by mass fraction, Si: 3.5%, magnesium: 0.01%) Use high-pressure roller mill iron ore powder to finely grind to obtain mixed iron ore concentrate powder, the -200 mesh particle size of mixed iron ore concentrate powder is 75%; magnesium-containing low-silicon iron ore concentrate powder: high-silicon iron ore concentrate powder=60: 40
[0054] 2) Mix iron concentrate powder and binder bentonite 98:2 to make a mixture, the weight ratio is: iron concentrate powder 98%, binder 2%;
[0055] 3) The mixture is subjected to high-pressure roller milling, drying to a moisture content of 9%, and then mixed with a powerful mixer;
[0056] 4) The mixture is made into pellets by adding water to the disc pelletizer, the amount of water added is 6% of the total amount of materials, and passed through a vibrating screen to...
PUM
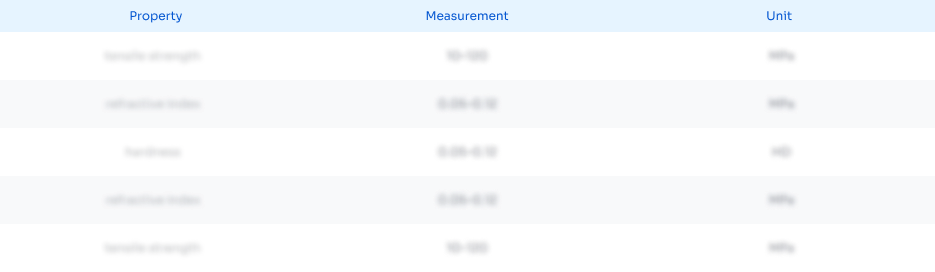
Abstract
Description
Claims
Application Information

- R&D
- Intellectual Property
- Life Sciences
- Materials
- Tech Scout
- Unparalleled Data Quality
- Higher Quality Content
- 60% Fewer Hallucinations
Browse by: Latest US Patents, China's latest patents, Technical Efficacy Thesaurus, Application Domain, Technology Topic, Popular Technical Reports.
© 2025 PatSnap. All rights reserved.Legal|Privacy policy|Modern Slavery Act Transparency Statement|Sitemap|About US| Contact US: help@patsnap.com