Antistatic injection molding material for preparing electronic parts
An anti-static and anti-static agent technology, applied in the field of injection molding materials, can solve the problems of high anti-static performance of injection molding materials, and achieve the effect of improving service life, use safety and strong anti-static performance
- Summary
- Abstract
- Description
- Claims
- Application Information
AI Technical Summary
Problems solved by technology
Method used
Examples
Embodiment 1
[0013] An anti-static injection molding material used to prepare electronic parts, including the following components by mass percentage:
[0014] Glyceryl stearate accounted for 12%, polycarbonate accounted for 16%, plasticizer accounted for 9%, lubricant accounted for 9%, antistatic agent accounted for 10%, and the rest was acrylonitrile-butadiene-styrene copolymer;
[0015] The antistatic agent is composed of a mixture of lignin, magnesium chloride, and aluminum chloride. Calculated by mass percentage, the content of magnesium chloride accounts for 8%, the content of aluminum chloride accounts for 20%, and the rest is lignin.
Embodiment 2
[0017] An anti-static injection molding material used to prepare electronic parts, including the following components by mass percentage:
[0018] Glyceryl stearate accounts for 18%, polycarbonate accounts for 20%, plasticizer accounts for 5%, lubricant accounts for 5%, antistatic agent accounts for 4%, and the rest is acrylonitrile-butadiene-styrene copolymer;
[0019] The antistatic agent is composed of a mixture of lignin, magnesium chloride, and aluminum chloride. According to mass percentage, the content of magnesium chloride accounts for 12%, the content of aluminum chloride accounts for 16%, and the rest is lignin.
Embodiment 3
[0021] An anti-static injection molding material used to prepare electronic parts, including the following components by mass percentage:
[0022] Glyceryl stearate accounted for 15%, polycarbonate accounted for 18%, plasticizer accounted for 7%, lubricant accounted for 7%, antistatic agent accounted for 7%, and the rest was acrylonitrile-butadiene-styrene copolymer;
[0023] The antistatic agent is composed of a mixture of lignin, magnesium chloride and aluminum chloride, and calculated by mass percentage, the content of magnesium chloride accounts for 10%, the content of aluminum chloride accounts for 18%, and the rest is lignin.
[0024] Wherein, the plasticizer is any one or more of phthalate esters, aliphatic dibasic acid esters, and phosphate esters, and the lubricant is paraffin wax, calcium stearate, hydrotalcite Any one or more mixtures.
[0025] The preparation method of an anti-static injection molding material for preparing electronic parts of the present invention is as f...
PUM
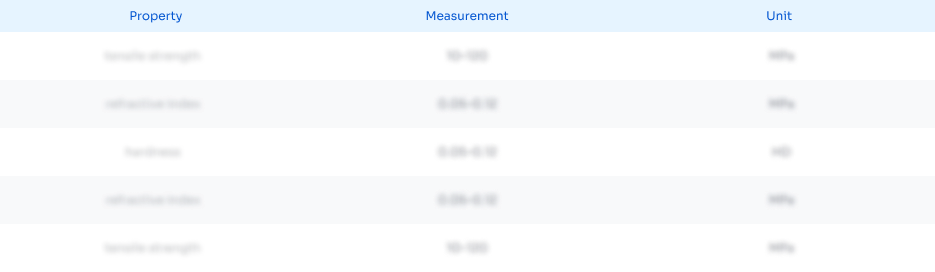
Abstract
Description
Claims
Application Information

- R&D Engineer
- R&D Manager
- IP Professional
- Industry Leading Data Capabilities
- Powerful AI technology
- Patent DNA Extraction
Browse by: Latest US Patents, China's latest patents, Technical Efficacy Thesaurus, Application Domain, Technology Topic, Popular Technical Reports.
© 2024 PatSnap. All rights reserved.Legal|Privacy policy|Modern Slavery Act Transparency Statement|Sitemap|About US| Contact US: help@patsnap.com