High-flame retardation polyethylene cable material and preparation method thereof
A polyethylene and cable material technology, applied in the direction of insulating cables, cables, circuits, etc., can solve the problems of poor flame retardancy, decreased mechanical properties, and obstacles to the promotion of polyethylene cable materials, and achieve high safety, low cost, outstanding resistance The effect of combustion performance and mechanical properties
- Summary
- Abstract
- Description
- Claims
- Application Information
AI Technical Summary
Problems solved by technology
Method used
Image
Examples
Embodiment 1
[0024] Example 1 A high flame-retardant polyethylene cable material is mainly prepared from the following raw materials (100kg per part): 110 parts of polyethylene, 16 parts of chlorinated paraffin, 4 parts of sulfur, 6 parts of epoxidized soybean oil, and 6 parts of diatomaceous earth , 5 parts of zinc borate, 8 parts of clay, 2 parts of dioctyl phthalate, 3 parts of white carbon black, 10 parts of aluminum hydroxide, 2 parts of stearic acid, 0.4 parts of dilauryl thiodipropionate.
[0025] A preparation method of high flame retardant polyethylene cable material is:
[0026] (1) Put aluminum hydroxide in an oven at 80°C and dry to constant weight at constant temperature, take it out, and pulverize it through a 60-mesh sieve;
[0027] (2) Place chlorinated paraffin, sulfur, zinc borate, clay, dioctyl phthalate and white carbon black in a mixer, stir and mix, then transfer to a grinder, and grind for 2 hours;
[0028] (3) Put polyethylene into the mixer, heat it with 0.2MPa...
Embodiment 2
[0030] Example 2 A high flame-retardant polyethylene cable material is mainly prepared from the following raw materials (100kg per part): 124 parts of polyethylene, 21 parts of chlorinated paraffin, 10 parts of sulfur, 11 parts of epoxidized soybean oil, and 12 parts of diatomite , 11 parts of zinc borate, 12 parts of clay, 6 parts of dioctyl phthalate, 6 parts of white carbon black, 16 parts of aluminum hydroxide, 4 parts of stearic acid, 0.8 parts of dilauryl thiodipropionate.
[0031] A preparation method of high flame retardant polyethylene cable material is:
[0032] (1) Put aluminum hydroxide in an oven at 80°C and dry to constant weight at a constant temperature, take it out, and smash it through a 100-mesh sieve;
[0033] (2) Place chlorinated paraffin, sulfur, zinc borate, clay, dioctyl phthalate and white carbon black in a mixer, stir and mix, then transfer to a grinder, and grind for 4 hours;
[0034] (3) Put polyethylene into the mixer, heat it with 0.4MPa stea...
Embodiment 3
[0036] Example 3 A high flame-retardant polyethylene cable material is mainly prepared from the following raw materials (100kg each): 114 parts of polyethylene, 18 parts of chlorinated paraffin, 6 parts of sulfur, 8 parts of epoxidized soybean oil, and 8 parts of diatomaceous earth , 7 parts of zinc borate, 9 parts of clay, 3 parts of dioctyl phthalate, 4 parts of white carbon black, 12 parts of aluminum hydroxide, 2.5 parts of stearic acid, 0.5 part of dilauryl thiodipropionate.
[0037] A preparation method of high flame retardant polyethylene cable material is:
[0038] (1) Put aluminum hydroxide in an oven at 80°C and dry to constant weight at a constant temperature, take it out, and pulverize it through a 70-mesh sieve;
[0039](2) Place chlorinated paraffin, sulfur, zinc borate, clay, dioctyl phthalate and white carbon black in a mixer, stir and mix, then transfer to a grinder, and grind for 2.5 hours;
[0040] (3) Put polyethylene into the mixer, heat it with 0.2MPa...
PUM
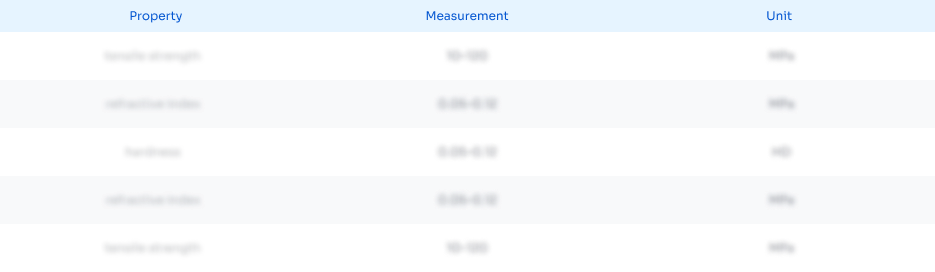
Abstract
Description
Claims
Application Information

- R&D
- Intellectual Property
- Life Sciences
- Materials
- Tech Scout
- Unparalleled Data Quality
- Higher Quality Content
- 60% Fewer Hallucinations
Browse by: Latest US Patents, China's latest patents, Technical Efficacy Thesaurus, Application Domain, Technology Topic, Popular Technical Reports.
© 2025 PatSnap. All rights reserved.Legal|Privacy policy|Modern Slavery Act Transparency Statement|Sitemap|About US| Contact US: help@patsnap.com