Plate-pipe composite heat-exchange fin and manufacturing method thereof
A production method and technology of heat exchange fins, applied in the direction of indirect heat exchangers, heat exchanger types, refrigerators, etc., can solve the problem that the heat exchange efficiency has not been improved to a maximum extent, and cannot meet the requirements of direct heat exchange, installation, Disassembly is cumbersome and other problems, to achieve the effect of increasing the cooling water evaporation area, reducing the volume of the condenser, and increasing the effective heat exchange area
- Summary
- Abstract
- Description
- Claims
- Application Information
AI Technical Summary
Problems solved by technology
Method used
Image
Examples
Embodiment Construction
[0032] In order to further elaborate the technical means and effects that the present invention adopts for reaching the intended invention purpose, below in conjunction with the accompanying drawings and preferred embodiments, the specific implementation, structure, features and effects of the present invention are described in detail as follows:
[0033] Such as figure 1 and figure 2 As shown, the plate-tube composite heat exchange fin of the present invention includes a coiled tube 1 processed by the heat exchange tube (the processing can be to bend the long heat exchange tube into a coil, or to bend the heat exchange tube of the bent section The tube is welded together with the heat exchange tube of the straight section to form a coil), and the heat transfer plate 2 is also included. In this embodiment, the coil 1 is formed by continuous S-shaped bending of the heat exchange tubes, and the straight sections of the heat exchange tubes are roughly parallel or not parallel. ...
PUM
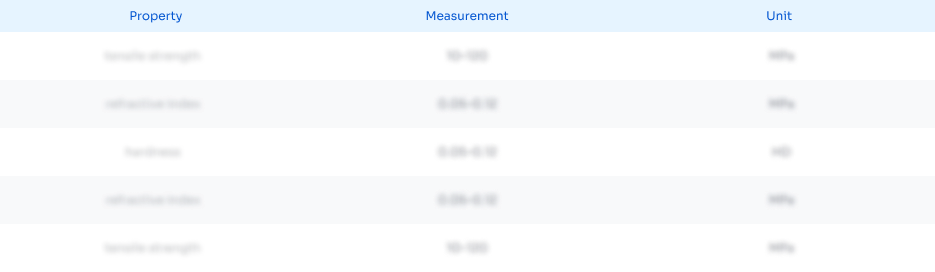
Abstract
Description
Claims
Application Information

- R&D
- Intellectual Property
- Life Sciences
- Materials
- Tech Scout
- Unparalleled Data Quality
- Higher Quality Content
- 60% Fewer Hallucinations
Browse by: Latest US Patents, China's latest patents, Technical Efficacy Thesaurus, Application Domain, Technology Topic, Popular Technical Reports.
© 2025 PatSnap. All rights reserved.Legal|Privacy policy|Modern Slavery Act Transparency Statement|Sitemap|About US| Contact US: help@patsnap.com