Double-layer refractory coating used for centrifugal casting process metal die and spraying process thereof
A technology of refractory coatings and metal molds, which is applied in the direction of manufacturing tools, metal processing equipment, tools, etc., can solve the problems that hinder the widespread application of centrifugal casting technology, prone to pores, slag inclusions, and difficult demoulding, etc., to achieve surface pores reduction, Easy mold taking and good surface quality
- Summary
- Abstract
- Description
- Claims
- Application Information
AI Technical Summary
Problems solved by technology
Method used
Examples
Embodiment Construction
[0014] A double-layer refractory coating for a centrifugal casting process metal mold, characterized in that the double-layer refractory coating includes a bottom refractory coating and a surface layer refractory coating, and the formula of the bottom refractory coating is 40%-50% graphite by mass percentage powder, 9-11% binder, 50%-40% water, the total amount of graphite powder, binder and water is 100%. The formula of the surface refractory coating is: 40%-50% mullite powder, 9-11% binder, 50%-40% water, the total amount of graphite powder, binder and water is 100%. Preferably, the mass percentage of the binder is 10%.
[0015] According to a preferred embodiment of the present invention, the particle size of the graphite powder is 500-1000 mesh.
[0016] According to a preferred embodiment of the present invention, the particle size of the mullite powder is 500-1000 mesh.
[0017] According to a preferred embodiment of the present invention, the total mass of the primer ...
PUM
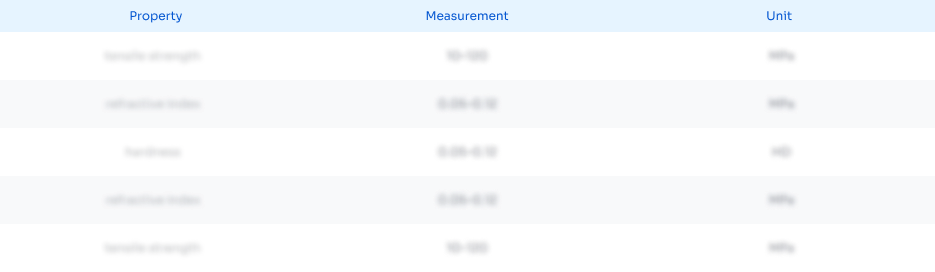
Abstract
Description
Claims
Application Information

- Generate Ideas
- Intellectual Property
- Life Sciences
- Materials
- Tech Scout
- Unparalleled Data Quality
- Higher Quality Content
- 60% Fewer Hallucinations
Browse by: Latest US Patents, China's latest patents, Technical Efficacy Thesaurus, Application Domain, Technology Topic, Popular Technical Reports.
© 2025 PatSnap. All rights reserved.Legal|Privacy policy|Modern Slavery Act Transparency Statement|Sitemap|About US| Contact US: help@patsnap.com