Finite element analysis method for thermal-coupled vibration characteristics of impeller structure
A technology of vibration characteristics and analysis methods, applied in special data processing applications, instruments, electrical digital data processing, etc., can solve blade breakage, rotor engine structural damage, aggravate the rubbing thermal shock effect between rotors and stators, and rotor dry friction instability. and other issues to achieve the effect of a reliable theoretical basis
- Summary
- Abstract
- Description
- Claims
- Application Information
AI Technical Summary
Problems solved by technology
Method used
Image
Examples
Embodiment Construction
[0013] The present invention will be further described with reference to the accompanying drawings and embodiments of the specification.
[0014] Such as figure 1 As shown, it is a working flow chart of the finite element analysis method for thermally coupled vibration characteristics of an impeller structure in the present invention. It mainly consists of two parts, which are respectively implemented by two softwares. The detailed steps are as follows:
[0015] Step 1: 3D modeling of the impeller structure, using the solidworks parametric modeling method for 3D modeling to obtain a 3D model of the impeller structure, such as figure 2 shown;
[0016] Step 2: Establish the finite element model of the impeller structure, import the 3D model of the impeller structure into the finite element analysis software ANSYS, and complete the design of material properties, parameters, loads and constraints in the pre-processing module of ANSYS software according to the actual working con...
PUM
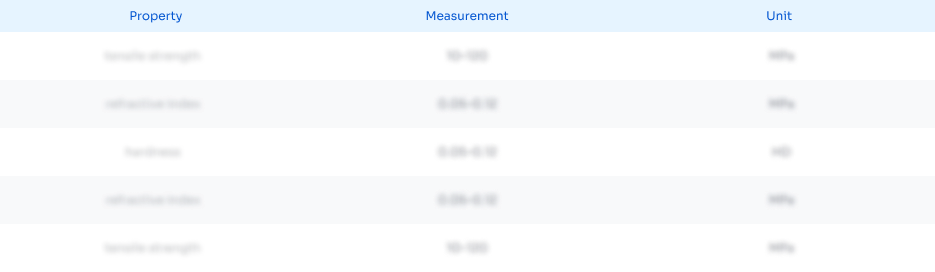
Abstract
Description
Claims
Application Information

- R&D
- Intellectual Property
- Life Sciences
- Materials
- Tech Scout
- Unparalleled Data Quality
- Higher Quality Content
- 60% Fewer Hallucinations
Browse by: Latest US Patents, China's latest patents, Technical Efficacy Thesaurus, Application Domain, Technology Topic, Popular Technical Reports.
© 2025 PatSnap. All rights reserved.Legal|Privacy policy|Modern Slavery Act Transparency Statement|Sitemap|About US| Contact US: help@patsnap.com