Kinetic model-based design method for fit clearance of machine tool spindle bearing
A dynamic model and machine tool spindle technology, applied in calculation, special data processing applications, instruments, etc., can solve problems such as the relationship that does not quantitatively reflect the rotation error of the spindle
- Summary
- Abstract
- Description
- Claims
- Application Information
AI Technical Summary
Problems solved by technology
Method used
Image
Examples
Embodiment Construction
[0053] The method for designing the fit clearance of the spindle bearing outer ring based on the dynamic model of the present invention will be further described in detail below in conjunction with an embodiment, but this embodiment is not intended to limit the present invention.
[0054] Such as figure 1 As shown, the present invention is based on the dynamic model of the machine tool spindle bearing fit clearance design method, comprising the following steps:
[0055] 1) According to the structure of the machine tool spindle, it is simplified into a bearing-rotor system to prepare for the establishment of the dynamic model of the machine tool spindle;
[0056] 2) According to the simplified bearing-rotor system in step 1), a dynamic model of the machine tool spindle is established.
[0057] The process of establishing the dynamic model of the machine tool spindle can be divided into three parts: the dynamic modeling of the spindle bearing, the rigid body element model of th...
PUM
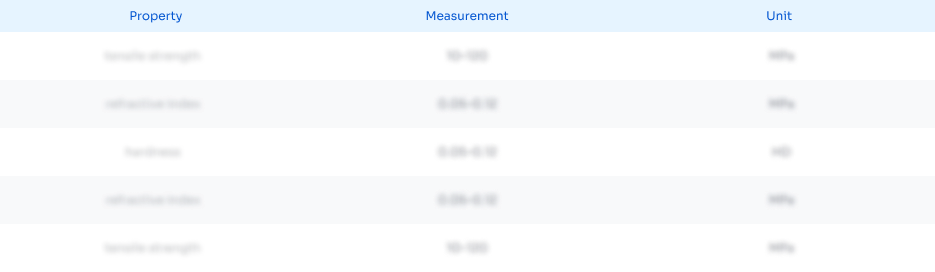
Abstract
Description
Claims
Application Information

- R&D Engineer
- R&D Manager
- IP Professional
- Industry Leading Data Capabilities
- Powerful AI technology
- Patent DNA Extraction
Browse by: Latest US Patents, China's latest patents, Technical Efficacy Thesaurus, Application Domain, Technology Topic, Popular Technical Reports.
© 2024 PatSnap. All rights reserved.Legal|Privacy policy|Modern Slavery Act Transparency Statement|Sitemap|About US| Contact US: help@patsnap.com