Six-axis joint robot distributed control system and method
A distributed control and robot technology, applied in the direction of digital control, electrical program control, etc., can solve problems such as complex implementation schemes, susceptibility to interference, and difficulty in troubleshooting and resolution, so as to be less susceptible to interference, reduce bandwidth requirements, reduce wiring and The effect of troubleshooting difficulty
- Summary
- Abstract
- Description
- Claims
- Application Information
AI Technical Summary
Problems solved by technology
Method used
Image
Examples
Embodiment Construction
[0020] The present invention will be described in more detail below in conjunction with the accompanying drawings and embodiments.
[0021] The invention discloses a distributed control system for a six-axis joint robot, which combines Figure 1 to Figure 5 As shown, it includes a six-axis articulated robot, a master station and five slave stations, and the master station and slave stations respectively correspond to six joints driving the six-axis articulated robot, wherein:
[0022] The master station is preset with a user program module, a PTP command execution module, a robot reverse solution calculation module, a communication control module, a virtual spindle module, an electronic cam module, and a motor control module. The user program module is used to execute the logic written by the user. Program, the logic program contains positioning instructions. When executing the positioning instructions, the PTP command execution module obtains the coordinates of the target poi...
PUM
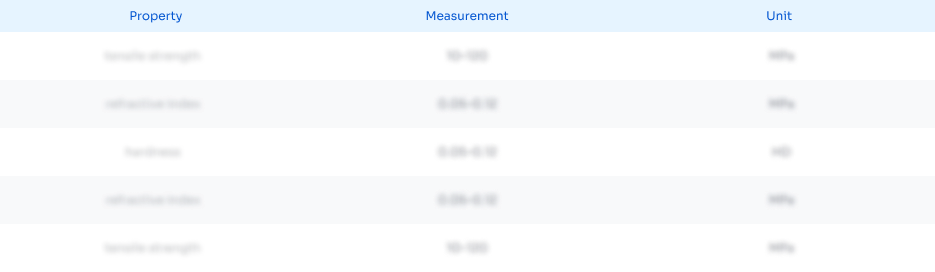
Abstract
Description
Claims
Application Information

- R&D Engineer
- R&D Manager
- IP Professional
- Industry Leading Data Capabilities
- Powerful AI technology
- Patent DNA Extraction
Browse by: Latest US Patents, China's latest patents, Technical Efficacy Thesaurus, Application Domain, Technology Topic, Popular Technical Reports.
© 2024 PatSnap. All rights reserved.Legal|Privacy policy|Modern Slavery Act Transparency Statement|Sitemap|About US| Contact US: help@patsnap.com