Production method of suede elastic fabric
A production method and fabric technology, applied to the surface trimming, weaving, yarn, etc. of the fabric, can solve the problems of easy generation of static electricity, decrease in strength, difficulty in dyeing, etc., and achieve the effect of soft hand feeling, good resilience, and obvious drape
- Summary
- Abstract
- Description
- Claims
- Application Information
AI Technical Summary
Problems solved by technology
Method used
Examples
Embodiment 1
[0018] For realizing above-mentioned technical effect, the production method of suede elastic fabric in embodiment 1 comprises the following steps:
[0019] S1: configure the raw material fiber of the fabric, the warp yarn and half of the weft yarn of the suede elastic fabric are made of wool and vinylon blended yarn, and the other half of the weft yarn is a core-spun yarn made of elastic fiber core yarn sorona staple fiber surface yarn; The content of vinylon in the yarn made by blending wool and vinylon is 5%;
[0020] S2: The above-mentioned fibers are respectively dyed and combed to make wool tops, and gray cloth is obtained through drawing, roving, spun yarn and weaving;
[0021] S3: The gray cloth obtained in S2 is returned, dried, brushed, sheared, shaped, steamed, and pre-shrunk. The pre-shrinking process parameters are: speed 5m / min, steam consumption 50%, overfeed 10 %.
[0022] The shearing process parameters are: 18m / min, the gauge is 0.7mm, and the shearing meth...
Embodiment 2
[0028] The difference between embodiment 2 and embodiment 1 is:
[0029] S1: The content of vinylon in the yarn prepared by blending wool and vinylon is 15%;
[0030] S3: The process parameters of pre-shrinking treatment are: vehicle speed 10m / min, steam consumption 75%, overfeed 10-15%.
[0031] The shearing process parameters are: 20m / min, the gauge is 1mm, and the shearing method is two fronts and one back.
[0032] The parameters of the debursing process are as follows: the desiccating temperature is 115°C, the time is 70s, the pressing roller pressure is 3.5 bar, and the wrapping tension is 90kg.
[0033] The finalizing treatment is shrinking on the machine, the shrinking range is 3%, the temperature is 170°C, and the speed is 18-22m / min.
[0034] The weight ratio of elastic fiber core yarn to sorona staple fiber surface yarn in core-spun yarn is 1:1.
[0035] The temperature for de-dimensionalizing treatment is 95°C.
Embodiment 3
[0037] The difference between embodiment 3 and embodiment 1 is:
[0038] S1: The content of vinylon in the yarn prepared by blending wool and vinylon is 10%;
[0039] S3: The process parameters of pre-shrinking treatment are: vehicle speed 7m / min, steam consumption 67%, overfeed 12%.
[0040] The shearing process parameters are: 19m / min, the gauge is 0.85mm, and the shearing method is two positive and one negative.
[0041] The parameters of the debursing process are as follows: the desiccating temperature is 110°C, the time is 60s, the pressing roller pressure is 3 bar, and the cloth tension is 75kg.
[0042] The finalizing treatment is shrinking on the machine, the shrinking range is 2.2%, the temperature is 165°C, and the speed is 20m / min.
[0043] The weight ratio of elastic fiber core yarn to sorona short fiber surface yarn in the core-spun yarn is 4:5.
[0044] The temperature for de-dimensionalizing treatment is 90°C.
PUM
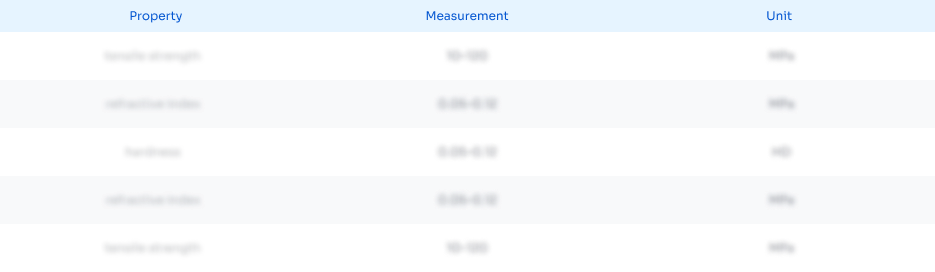
Abstract
Description
Claims
Application Information

- R&D
- Intellectual Property
- Life Sciences
- Materials
- Tech Scout
- Unparalleled Data Quality
- Higher Quality Content
- 60% Fewer Hallucinations
Browse by: Latest US Patents, China's latest patents, Technical Efficacy Thesaurus, Application Domain, Technology Topic, Popular Technical Reports.
© 2025 PatSnap. All rights reserved.Legal|Privacy policy|Modern Slavery Act Transparency Statement|Sitemap|About US| Contact US: help@patsnap.com