Rubber plastic material for elevator and preparation method thereof
A rubber-plastic and elevator technology, applied in the field of rubber, can solve problems such as low stiffness and poor dynamic performance, and achieve the effects of increasing rubber-plastic performance, shortening vulcanization time, and increasing service life
- Summary
- Abstract
- Description
- Claims
- Application Information
AI Technical Summary
Problems solved by technology
Method used
Examples
Embodiment 1
[0018] A rubber and plastic material for elevators and a preparation method thereof, comprising the following steps:
[0019] S1. Take 40-50 parts of natural rubber and 60-75 parts of styrene-butadiene rubber, and masticate at a temperature of 50-70 ° C for 1-2 hours;
[0020] S2. Put the masticated rubber in the refining furnace, and take 5-13 parts of pottery clay, 8-15 parts of medical stone, and 10-14 parts of carbon black into the refining furnace, and put them together at a temperature of 35-45°C Aging for 4-6 hours;
[0021] S3. Take 5-15 parts of high styrene resin, 10-15 parts of dioctyl sebacate, 6-12 parts of phenolic resin, 15-20 parts of zinc oxide, and 10-15 parts of sulfur into the furnace. Mixing at 75°C for 20-30 minutes;
[0022] S4. After 20-30 minutes, take 10-14 parts of vulcanization accelerator, 12-15 parts of stearic acid, 13-16 parts of boric acid, 15-18 parts of crosslinking agent, and 15-21 parts of surfactant into the furnace , kneading at a temp...
Embodiment 2
[0024] A rubber and plastic material for elevators and a preparation method thereof, comprising the following steps:
[0025] S1. Take 40 parts of natural rubber and 60 parts of styrene-butadiene rubber, and masticate at a temperature of 50-70° C. for 1-2 hours;
[0026] S2. Put the masticated rubber in the refining furnace, and take 5 parts of pottery clay, 8-parts of medical stone, and 10 parts of carbon black into the refining furnace, and age them together for 4-6 hours at a temperature of 35-45°C ;
[0027] S3. Take 5 parts of high-styrene resin, 10 parts of dioctyl sebacate, 6 parts of phenolic resin, 15 parts of zinc oxide, and 10 parts of sulfur into the furnace, and knead at a temperature of 60-75 ° C for 20 minutes;
[0028] S4. After 20-30 minutes, take 10 parts of vulcanization accelerator, 12 parts of stearic acid, 13 parts of boric acid, 15 parts of crosslinking agent, and 15 parts of surfactant into the furnace, and mix them at a temperature of 80-100°C. Refin...
Embodiment 3
[0030] A rubber and plastic material for elevators and a preparation method thereof, comprising the following steps:
[0031] S1. Take 42 parts of natural rubber and 63 parts of styrene-butadiene rubber, and masticate at a temperature of 50-70° C. for 1-2 hours;
[0032] S2. Put the masticated rubber in the refining furnace, and take 9 parts of pottery clay, 10 parts of medical stone, and 12 parts of carbon black into the refining furnace, and ripen together for 4-6 hours at a temperature of 35-45°C;
[0033] S3. Take 7 parts of high styrene resin, 12 parts of dioctyl sebacate, 8 parts of phenolic resin, 17 parts of zinc oxide, and 13 parts of sulfur into the furnace, and mix at a temperature of 60-75 ° C for 20-30 minute;
[0034] S4. After 20-30 minutes, take 11 parts of vulcanization accelerator, 13 parts of stearic acid, 14 parts of boric acid, 17 parts of cross-linking agent, and 18 parts of surfactant into the furnace, and mix them at a temperature of 80-100°C. Refined...
PUM
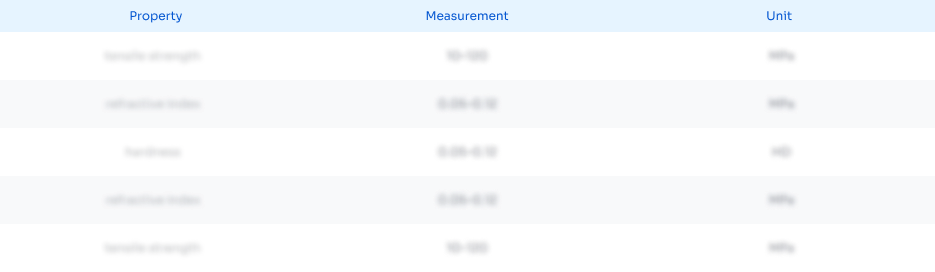
Abstract
Description
Claims
Application Information

- R&D Engineer
- R&D Manager
- IP Professional
- Industry Leading Data Capabilities
- Powerful AI technology
- Patent DNA Extraction
Browse by: Latest US Patents, China's latest patents, Technical Efficacy Thesaurus, Application Domain, Technology Topic, Popular Technical Reports.
© 2024 PatSnap. All rights reserved.Legal|Privacy policy|Modern Slavery Act Transparency Statement|Sitemap|About US| Contact US: help@patsnap.com