Improvement of longitudinal isolation strip of metalized safety membrane electrode
A technology of metallization and safety film, applied in the direction of fixed capacitor electrodes, parts of fixed capacitors, capacitors, etc., can solve problems such as continuous fusing, spreading, and breakdown points that cannot be safely self-healed
- Summary
- Abstract
- Description
- Claims
- Application Information
AI Technical Summary
Problems solved by technology
Method used
Image
Examples
Embodiment 1
[0022] Example 1 is an improvement of a metalized safety composite film with a T-shaped electrode structure vapor deposited on a polypropylene dielectric material. One side of the composite film is a margin 2.1 and a width of 2.5mm; the other side is a thickened coating Side 1.1, width 2.2mm; the horizontal gap strips 2.11 and the longitudinal gap strips 2.12 and the margins together separate the electrode coating on the membrane surface into a row of longitudinally arranged small electrode units 1.12, forming a metalized safety composite film with a T-shaped electrode structure ( Such as figure 1 with figure 2 (Shown); In this embodiment: the width of the gap strips 2.11 and 2.12 are both 0.5 mm, the longitudinal length of the small electrode unit 1.12 is 25 mm, and the width of the plating narrow strip 1.11 of the fuse is 0.5 mm. in figure 1 All the longitudinal gap strips 2.12 are arranged in a straight line, and the oil recovery width of the printed graphics is equal to the...
Embodiment 2
[0024] Example 2 Improvement of the metalized safety composite film with a grid electrode structure vapor-deposited on a polypropylene dielectric material. One side of the composite film is a margin 2.1 and a width of 2.0mm; the other side is a thickened coating Side 1.1, width 2.2mm; The oblique gap strip 2.13, the longitudinal gap strip 2.12 and the margin together separate the electrode coating on the membrane surface into many small electrode units 1.12, forming a metalized safety composite membrane with a grid electrode structure (such as image 3 , 4 Show). In this embodiment: the width of the coating strip 1.11 of the fuse is 0.3mm, the diagonal gap strip 2.13 has a width of 0.3mm, and the longitudinal gap strip 2.12 has a width of 0.6mm and a length of 10mm; image 3 All the longitudinal gap strips 2.12 are arranged in a straight line. The longitudinal gap strip 2.12 separates a row of longitudinally arranged triangular small electrode units from the coating thickened sid...
PUM
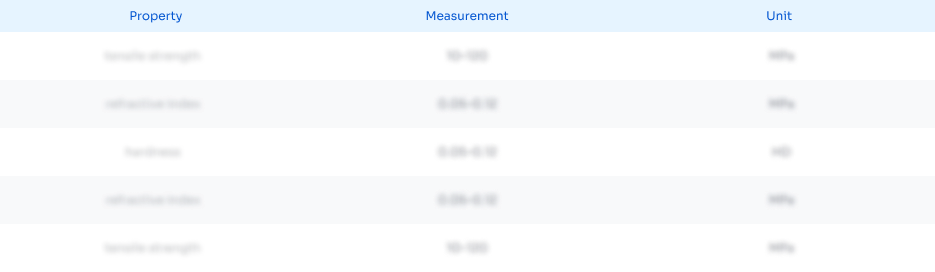
Abstract
Description
Claims
Application Information

- Generate Ideas
- Intellectual Property
- Life Sciences
- Materials
- Tech Scout
- Unparalleled Data Quality
- Higher Quality Content
- 60% Fewer Hallucinations
Browse by: Latest US Patents, China's latest patents, Technical Efficacy Thesaurus, Application Domain, Technology Topic, Popular Technical Reports.
© 2025 PatSnap. All rights reserved.Legal|Privacy policy|Modern Slavery Act Transparency Statement|Sitemap|About US| Contact US: help@patsnap.com