Robot joint motor synchronization control system and method
A robot joint, synchronous control technology, applied in the field of synchronous control system and robot joint motor synchronous control system, can solve the problems of clock running asynchronous, clock drift, delay, etc., to achieve the effect of improving synchronization performance and improving the accuracy of motion trajectory
- Summary
- Abstract
- Description
- Claims
- Application Information
AI Technical Summary
Problems solved by technology
Method used
Image
Examples
Embodiment 1
[0045] Embodiment 1: as figure 1 with figure 2 As shown, a robot joint motor synchronous control system, including embedded microprocessor, servo driver, EtherCAT bus and EtherCAT slave station controller;
[0046] The embedded microprocessor is provided with an Ethernet controller, which is connected with the EtherCAT slave station controller through the EtherCAT bus, and the EtherCAT slave station controller is connected with the servo driver.
[0047] The first EtherCAT slave connected to the embedded microprocessor as a reference clock slave;
[0048] The EtherCAT slave station controller contains 4 data transceiver ports, and the receiving time of each port is stored in 4 different registers, and the local clock time when the data frame arrives at the port 0-4 is respectively saved in the port 0-4 register;
[0049] Described EtherCAT slave station controller contains local system time register, stores the local system time when each data frame arrives;
[0050] The E...
PUM
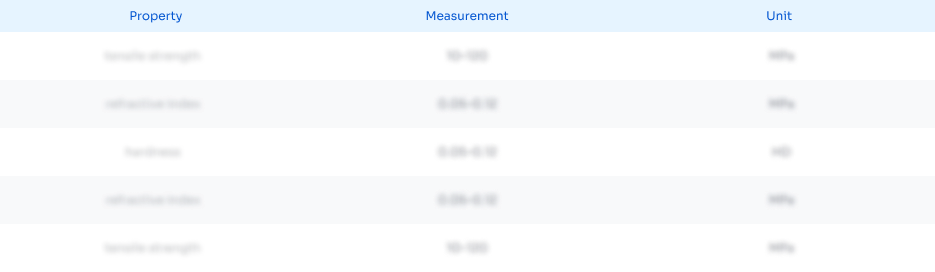
Abstract
Description
Claims
Application Information

- Generate Ideas
- Intellectual Property
- Life Sciences
- Materials
- Tech Scout
- Unparalleled Data Quality
- Higher Quality Content
- 60% Fewer Hallucinations
Browse by: Latest US Patents, China's latest patents, Technical Efficacy Thesaurus, Application Domain, Technology Topic, Popular Technical Reports.
© 2025 PatSnap. All rights reserved.Legal|Privacy policy|Modern Slavery Act Transparency Statement|Sitemap|About US| Contact US: help@patsnap.com