Thermal treatment method for large-section axle-type forge pieces
A heat treatment method and large cross-section technology, applied in the field of heat treatment, can solve the problems of steam film generation, failure to meet the process requirements of rapid cooling and uniform cooling, and the inability to adjust the cooling speed in the air cooling chamber, so as to achieve the effect of high strength and toughness
- Summary
- Abstract
- Description
- Claims
- Application Information
AI Technical Summary
Problems solved by technology
Method used
Image
Examples
Embodiment Construction
[0014] The heat treatment method for a large-section shaft forging provided by the present invention will be described in detail below in conjunction with the accompanying drawings and specific embodiments.
[0015] The heat treatment method for a large-section shaft forging provided by the present invention includes the following steps in order:
[0016] 1) Normalize the large cross-section shaft forgings at a heating rate of 4-7°C / min, then hold at a temperature of 910-930°C for 220-260 minutes, and then wind them at a cooling rate of 60-70°C / min. Cool to 500-600°C, and then air-cool to below 150°C at a cooling rate of 5-10°C / min; in this step, known heating equipment can be used to normalize and heat-preserve the forgings, and then use the graded controllable jet flow method Air-cooling is used for cooling. For example, a high-pressure fan can be used to drive cold air into the angle-shaped static pressure box, and the cold air can be evenly sprayed on the surface of the fo...
PUM
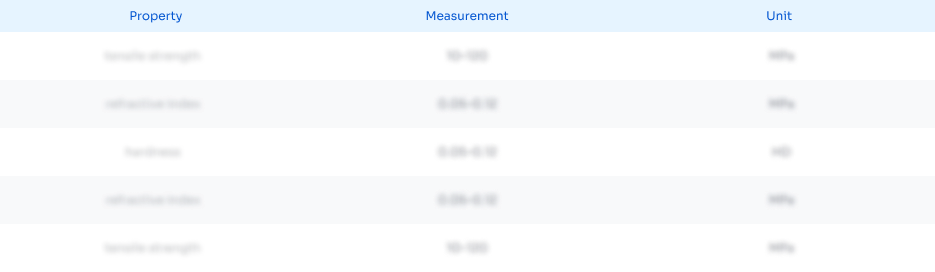
Abstract
Description
Claims
Application Information

- R&D
- Intellectual Property
- Life Sciences
- Materials
- Tech Scout
- Unparalleled Data Quality
- Higher Quality Content
- 60% Fewer Hallucinations
Browse by: Latest US Patents, China's latest patents, Technical Efficacy Thesaurus, Application Domain, Technology Topic, Popular Technical Reports.
© 2025 PatSnap. All rights reserved.Legal|Privacy policy|Modern Slavery Act Transparency Statement|Sitemap|About US| Contact US: help@patsnap.com