Wear-resistant hollow plate and production method thereof
A plate and hollow technology is applied in the field of wear-resistant hollow plates and their preparation, which can solve the problems of lack of wear resistance, and achieve the effects of good wear resistance, simple process and low cost.
- Summary
- Abstract
- Description
- Claims
- Application Information
AI Technical Summary
Problems solved by technology
Method used
Image
Examples
Embodiment 1
[0020] A wear-resistant hollow plate, which is composed of the following components in proportion by weight: 18 parts of polycaprolactone, 18 parts of polyethylene, 9 parts of polypropylene, 8 parts of acrylic resin, 18 parts of dialdehyde starch, silicon dioxide 7 parts, glass fiber 9 parts, glycerin 9 parts, sodium chloride 7 parts, sodium hydroxide 3 parts, isopropanol 7 parts, water 19 parts.
[0021] A method for preparing a wear-resistant hollow plate, comprising the following steps:
[0022] (1) Add dialdehyde starch, silicon dioxide, glass fiber, and sodium hydroxide into water, and stir evenly at a temperature of 55°C and a pH value of 8.7 to make a paste; add the paste mixture into the autoclave , reacted for 35 minutes under the condition of 3.2MPa;
[0023] (2) Add polycaprolactone, polyethylene, polypropylene, and acrylic resin to isopropanol, place in a high-pressure reactor, and react under sealed conditions at 278°C for 30 minutes;
[0024] (3) Dissolve glyce...
Embodiment 2
[0027] A wear-resistant hollow plate, which is composed of the following components in proportion by weight: 33 parts of polycaprolactone, 27 parts of polyethylene, 16 parts of polypropylene, 13 parts of acrylic resin, 28 parts of dialdehyde starch, silicon dioxide 17 parts, glass fiber 19 parts, glycerin 15 parts, sodium chloride 14 parts, sodium hydroxide 8 parts, isopropanol 22 parts, water 35 parts.
[0028] A method for preparing a wear-resistant hollow plate, comprising the following steps:
[0029] (1) Add dialdehyde starch, silicon dioxide, glass fiber, and sodium hydroxide into water, and stir evenly at a temperature of 68°C and a pH value of 10.8 to make a paste; add the paste mixture into a high-pressure reactor , reacted for 44 minutes under the condition of 4.2MPa;
[0030] (2) Add polycaprolactone, polyethylene, polypropylene, and acrylic resin to isopropanol, place in a high-pressure reactor, and react at 368°C for 54 minutes under sealed conditions;
[0031] ...
Embodiment 3
[0034] A wear-resistant hollow plate, which is composed of the following components in proportion by weight: 38 parts of polycaprolactone, 32 parts of polyethylene, 22 parts of polypropylene, 17 parts of acrylic resin, 34 parts of dialdehyde starch, silicon dioxide 23 parts, glass fiber 24 parts, glycerin 21 parts, sodium chloride 18 parts, sodium hydroxide 11 parts, isopropanol 25 parts, water 39 parts.
[0035] A method for preparing a wear-resistant hollow plate, comprising the following steps:
[0036] (1) Add dialdehyde starch, silicon dioxide, glass fiber, and sodium hydroxide into water, and stir evenly at a temperature of 85°C and a pH value of 11.3 to make a paste; add the paste mixture into a high-pressure reactor , reacted for 50 minutes under the condition of 4.8MPa;
[0037] (2) Add polycaprolactone, polyethylene, polypropylene, and acrylic resin to isopropanol, place in a high-pressure reactor, and react under sealed conditions at 395°C for 65 minutes;
[0038]...
PUM
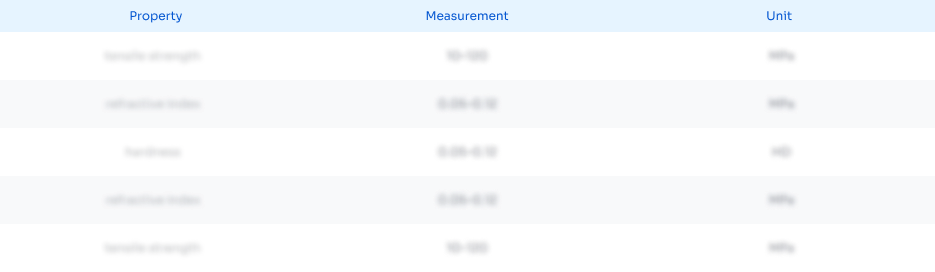
Abstract
Description
Claims
Application Information

- Generate Ideas
- Intellectual Property
- Life Sciences
- Materials
- Tech Scout
- Unparalleled Data Quality
- Higher Quality Content
- 60% Fewer Hallucinations
Browse by: Latest US Patents, China's latest patents, Technical Efficacy Thesaurus, Application Domain, Technology Topic, Popular Technical Reports.
© 2025 PatSnap. All rights reserved.Legal|Privacy policy|Modern Slavery Act Transparency Statement|Sitemap|About US| Contact US: help@patsnap.com