Hydraulic hollow tube springback control method and device
A control method and hollow tube technology, applied in the field of pipe fitting parts manufacturing, can solve problems such as long modeling period of combined bends, difficulty in predicting springback trend, impact on product quality, etc., to eliminate springback, reduce wear, and improve dimensional accuracy Effect
- Summary
- Abstract
- Description
- Claims
- Application Information
AI Technical Summary
Problems solved by technology
Method used
Image
Examples
Embodiment 1
[0024] Such as image 3 As shown, a hydraulic hollow pipe springback control device is composed of several independent mold cavity sections 1, and two adjacent mold cavity sections 1 are hingedly connected by a rotating shaft 2, and the rotating shaft The axis of 2 is the rotation center corresponding to the bending part of the machined part, and the rebound adjustment mechanism 3 is arranged on the mold cavity section 1 .
[0025] In this embodiment, the mold cavity section 1 has three sections in total, and the three mold cavity sections 1 are sequentially spliced to form two bends in the same direction, and the rebound adjustment mechanism 3 is arranged at two Between side mold cavity segments 1.
[0026] In order to cooperate with the three-stage structure in this embodiment, it is convenient to adjust the bending angle, such as Figure 4 As shown, the rebound adjustment mechanism 3 includes an adjustment screw 31 and a pair of adjustment nuts 32, and a pair of mold ca...
PUM
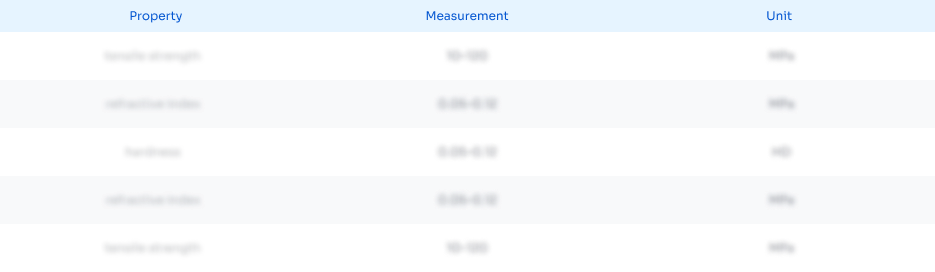
Abstract
Description
Claims
Application Information

- Generate Ideas
- Intellectual Property
- Life Sciences
- Materials
- Tech Scout
- Unparalleled Data Quality
- Higher Quality Content
- 60% Fewer Hallucinations
Browse by: Latest US Patents, China's latest patents, Technical Efficacy Thesaurus, Application Domain, Technology Topic, Popular Technical Reports.
© 2025 PatSnap. All rights reserved.Legal|Privacy policy|Modern Slavery Act Transparency Statement|Sitemap|About US| Contact US: help@patsnap.com