Preparation method of functional magnesium hydroxide flame retardant and flame retardant prepared through method
A magnesium hydroxide, functional technology, applied in the field of flame retardants, can solve the problems of high cost, magnesium hydroxide flame retardant combination, large filling amount, etc. Effect
- Summary
- Abstract
- Description
- Claims
- Application Information
AI Technical Summary
Problems solved by technology
Method used
Examples
preparation example Construction
[0023] The invention provides a method for preparing a functional magnesium hydroxide flame retardant, the method comprising: a. mixing water, ethanol and ethylene glycol according to a mass ratio of 1: (0.1-0.3): (0.05-0.2), Obtain a solvent; b, dissolve the magnesium salt in the solvent to obtain a magnesium salt solution with a mass concentration of 2-10%; c, be 100:(0.5-5) to the magnesium salt according to the mass ratio of the magnesium salt and the surfactant A surfactant is added to the magnesium salt solution to obtain the first liquid, and the first liquid is ultrasonically placed into a water bath container with a constant temperature, while the first liquid is kept stirring at a constant speed, and the water bath container maintains a water bath temperature of 15- 35 degrees Celsius; d, the mass concentration of 2-10% ammonia solution is added dropwise to the first liquid under stirring until the pH of the mixed solution is 9.5-10, and the mixed solution is kept und...
Embodiment 1
[0036] a. Mix water, ethanol and ethylene glycol according to the mass ratio of 1:0.1:0.05 to obtain a solvent; b. Dissolve magnesium nitrate in the solvent to obtain a magnesium salt solution with a mass concentration of 2%; c. The mass ratio of magnesium salt and surfactant is 100:0.5. Add surfactant PEG-800 to the magnesium salt solution to obtain the first liquid. After the first liquid is subjected to ultrasound at a frequency of 25KHZ for 20 minutes, it is placed in a temperature of 15 degrees Celsius. Keep stirring at a constant speed of 600 rpm in a water bath container; d. Add ammonia solution with a mass concentration of 2% to the first liquid under stirring until the pH of the mixed solution is 9.5, and adjust the water bath while the mixed solution is kept stirring. The temperature of the container is 40 degrees Celsius, and the second liquid is obtained after reacting for 30 minutes; e. After the second liquid is left to stand at room temperature for 1 hour, it is ...
Embodiment 2
[0038]a. Mix water, ethanol and ethylene glycol according to the mass ratio of 1:0.3:0.2 to obtain a solvent; b. Dissolve magnesium chloride in the solvent to obtain a magnesium salt solution with a mass concentration of 10%; c. The mass ratio of salt to surfactant is 100:5. Add surfactant PEG-1000 to the magnesium salt solution to obtain the first liquid. After the first liquid is ultrasonicated at 130KHZ for 1 hour, it is placed in a water bath container with a temperature of 35 degrees Celsius. and keep stirring at a constant speed of 1500 rev / min; d, adding the ammonia solution with a mass concentration of 10% dropwise into the first liquid under stirring until the pH of the mixed solution is 10, and keep the mixed solution under stirring to adjust the water bath container The temperature is 90 degrees centigrade, and the second liquid is obtained after reacting for 2 hours; e, the second liquid is left to stand at room temperature for 6 hours and then washed with water for...
PUM
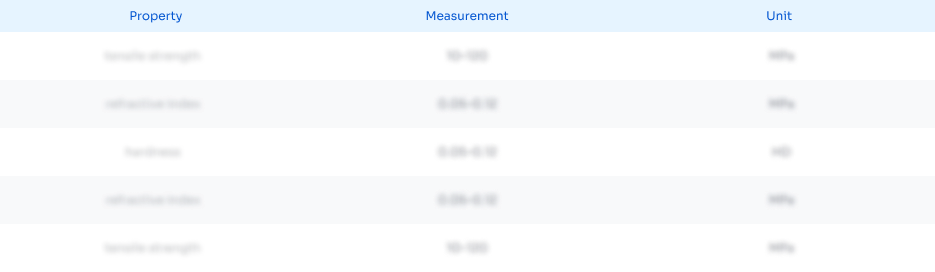
Abstract
Description
Claims
Application Information

- R&D Engineer
- R&D Manager
- IP Professional
- Industry Leading Data Capabilities
- Powerful AI technology
- Patent DNA Extraction
Browse by: Latest US Patents, China's latest patents, Technical Efficacy Thesaurus, Application Domain, Technology Topic, Popular Technical Reports.
© 2024 PatSnap. All rights reserved.Legal|Privacy policy|Modern Slavery Act Transparency Statement|Sitemap|About US| Contact US: help@patsnap.com