A kind of double capsule self-healing epoxy coating and preparation method thereof
An epoxy coating and self-repairing technology, which is applied in the direction of microcapsule preparation, microsphere preparation, etc., can solve the problems of inability to provide sufficient structural stability, emulsion droplet fusion, low encapsulation efficiency, emulsion breaking, etc., and achieve improved repair Efficiency, increased package volume, and high production efficiency
- Summary
- Abstract
- Description
- Claims
- Application Information
AI Technical Summary
Problems solved by technology
Method used
Image
Examples
Embodiment 1
[0028] (1) Add 1 g of polyvinyl alcohol (polymerization degree: 2600) to 100 mL of deionized water, and stir magnetically at 80 °C for 12 h to obtain an aqueous solution of polyvinyl alcohol. Add 30 mg of silica nanoparticles to 6 mL of polyvinyl alcohol aqueous solution for ultrasonic dispersion for 1 min, add 3 g of epoxy resin, mix the oil and water phases, and emulsify at 9000 rpm high-speed shear to obtain a stable oil-in-water picogram of silica nanoparticles Lin emulsion; then add 300 ml of isophorone diisocyanate to the Pickering emulsion, and mix well to obtain a mixed solution. Dissolve 300 mL of tetraethylenepentamine in 3 mL of deionized water, then add it into the mixture, and let it stand at room temperature for 40 min to obtain a suspension of epoxy microcapsules, wash the suspension three times with water, filter, and dry at room temperature for 24 h , to obtain epoxy microcapsules.
[0029] (2) Add 1 g polyisobutylene (molecular weight: 2400) to 100 mL xylene...
Embodiment 2
[0032](1) Add 1 g of polyvinyl alcohol (polymerization degree: 2600) to 100 mL of deionized water, and stir magnetically at 80 °C for 12 h to obtain an aqueous solution of polyvinyl alcohol. Add 30 mg of silica nanoparticles to 6 mL of polyvinyl alcohol aqueous solution for ultrasonic dispersion for 1 min, add 1.8 g of epoxy resin, mix the oil and water phases, and emulsify at a high speed of 3000 rpm to obtain a stable oil-in-water picogram of silica nanoparticles. forest lotion. Then add 180 mL of isophorone diisocyanate to the Pickering emulsion, and mix evenly to obtain a mixed solution. After dissolving 150 mL tetraethylenepentamine in 3 mL deionized water, add it to the mixture. Stand at room temperature for 40 min to obtain a suspension of epoxy microcapsules, wash the suspension three times with water, filter, and dry at room temperature for 24 h to obtain epoxy microcapsules.
[0033] (2) Add 1 g polyisobutylene (molecular weight: 2400) to 100 mL xylene, and stir ma...
Embodiment 3
[0036] (1) Add 1 g of polyvinyl alcohol (polymerization degree: 2600) to 100 mL of deionized water, and stir magnetically at 80 °C for 12 h to obtain an aqueous solution of polyvinyl alcohol. Add 30 mg of silicon dioxide nanoparticles to 6 mL of polyvinyl alcohol aqueous solution for ultrasonic dispersion for 1 min, add 4.2 g of epoxy resin, mix the oil and water phases, and emulsify at 6000 rpm high-speed shear to obtain silicon dioxide nanoparticles stabilized oil-in-water pg forest lotion. Add 480 mL of isophorone diisocyanate to the Pickering emulsion, and mix evenly to obtain a mixed solution. Dissolve 450 mL of tetraethylenepentamine in 3 ml of deionized water, and then add it to the mixture. Stand at room temperature for 40 min to obtain a suspension of epoxy microcapsules, wash the suspension three times with water, filter, and dry at room temperature for 24 h to obtain epoxy microcapsules.
[0037] (2) Add 1 g polyisobutylene (molecular weight: 2400) to 100 mL xylen...
PUM
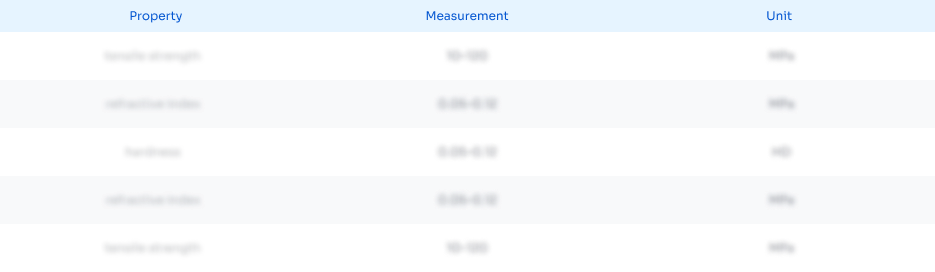
Abstract
Description
Claims
Application Information

- R&D
- Intellectual Property
- Life Sciences
- Materials
- Tech Scout
- Unparalleled Data Quality
- Higher Quality Content
- 60% Fewer Hallucinations
Browse by: Latest US Patents, China's latest patents, Technical Efficacy Thesaurus, Application Domain, Technology Topic, Popular Technical Reports.
© 2025 PatSnap. All rights reserved.Legal|Privacy policy|Modern Slavery Act Transparency Statement|Sitemap|About US| Contact US: help@patsnap.com