Robot zero calibration system and method based on laser triangulation ranging
A technology of laser triangulation distance measurement and zero calibration, which is applied in the directions of distance measurement, surveying and navigation, instruments, etc. It can solve the problems of low position and posture measurement accuracy, heavy weight, and difficulty in achieving spatial position measurement accuracy, and achieve calibration The effect of high precision and good versatility
- Summary
- Abstract
- Description
- Claims
- Application Information
AI Technical Summary
Problems solved by technology
Method used
Image
Examples
Embodiment Construction
[0037] The present invention will be described in detail below in conjunction with specific embodiments. The following examples will help those skilled in the art to further understand the present invention, but do not limit the present invention in any form. It should be pointed out that for those of ordinary skill in the art, a number of modifications and improvements can be made without departing from the concept of the present invention. These all belong to the protection scope of the present invention.
[0038] Such as figure 1 As shown, a robot zero calibration system based on laser triangulation distance measurement consists of a first calibrator 1, a first calibrator 2, a first calibrator 3, a first target 4, a second target 5, and a third target 6. , And a controller 8, wherein: the first calibrator 1, the first calibrator 2, the first calibrator 3 are respectively arranged on a rigid base at any position around the robot body 7 environment; the first target 4, the firs...
PUM
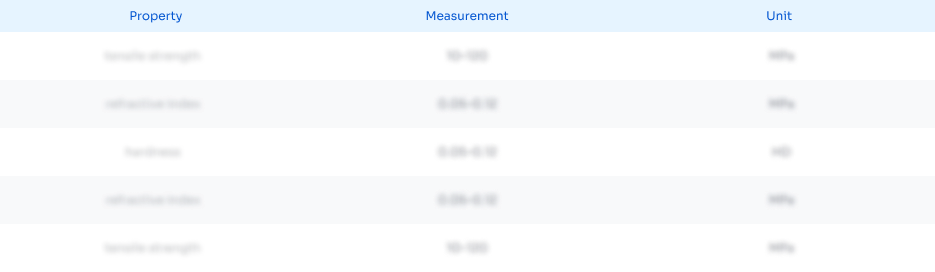
Abstract
Description
Claims
Application Information

- R&D
- Intellectual Property
- Life Sciences
- Materials
- Tech Scout
- Unparalleled Data Quality
- Higher Quality Content
- 60% Fewer Hallucinations
Browse by: Latest US Patents, China's latest patents, Technical Efficacy Thesaurus, Application Domain, Technology Topic, Popular Technical Reports.
© 2025 PatSnap. All rights reserved.Legal|Privacy policy|Modern Slavery Act Transparency Statement|Sitemap|About US| Contact US: help@patsnap.com