Hand-eye calibration method employing two-dimension laser vision sensor and robot
A visual sensor, two-dimensional laser technology, applied in instruments, measuring devices, etc., can solve problems such as poor practicability and performance interference
- Summary
- Abstract
- Description
- Claims
- Application Information
AI Technical Summary
Problems solved by technology
Method used
Image
Examples
Embodiment
[0093] A two-dimensional laser sensor is installed on the end flange of the robot (including robot controller and teaching box) through the mounting bracket. The sensor communicates with the computer, and the computer receives the measurement data returned by the sensor.
[0094] When the laser beam emitted by the two-dimensional laser sensor is projected onto the surface of the measured object, the laser beam will form an image consistent with the surface contour of the measured object. There are a series of continuous and uniformly distributed P laser sampling points on the laser beam. Then the sensor returns the Z-axis and X-axis coordinate values of the P sampling points in the laser beam relative to the sensor measurement coordinate system.
[0095] Combined with the calibration board, laser sensors and robots are used to obtain the data required for hand-eye calibration. The method also uses a computer to obtain the measurement data of the two-dimensional laser sensor,...
PUM
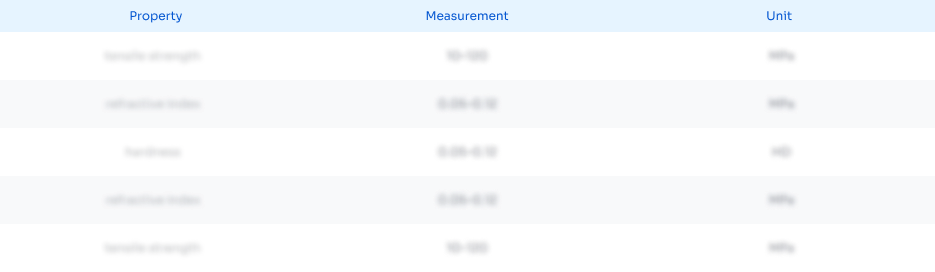
Abstract
Description
Claims
Application Information

- R&D
- Intellectual Property
- Life Sciences
- Materials
- Tech Scout
- Unparalleled Data Quality
- Higher Quality Content
- 60% Fewer Hallucinations
Browse by: Latest US Patents, China's latest patents, Technical Efficacy Thesaurus, Application Domain, Technology Topic, Popular Technical Reports.
© 2025 PatSnap. All rights reserved.Legal|Privacy policy|Modern Slavery Act Transparency Statement|Sitemap|About US| Contact US: help@patsnap.com