A kind of continuous production process of 3,6-dichlorosalicylic acid
A technology of dichlorosalicylic acid and production process, which is applied in the field of intermediates for synthesizing herbicide dicamba, can solve the problems of low production efficiency and product yield, harsh water content requirements, and high equipment investment costs, and achieves reduction of side reactions. The effect of reducing the generation of high temperature and high pressure reactors and reducing equipment investment costs
- Summary
- Abstract
- Description
- Claims
- Application Information
AI Technical Summary
Problems solved by technology
Method used
Image
Examples
Embodiment 1
[0045] A continuous production process of 3,6-dichlorosalicylic acid includes the following process steps:
[0046] A. Stir and mix the xylene solution of potassium 2,5-dichlorophenate, anhydrous potassium carbonate powder, and dispersant in the batching kettle to obtain a slurry;
[0047] B. The slurry in step A is pumped into the carbon dioxide absorption tank through a metering pump, the carbon dioxide gas source is turned on, and the carbon dioxide gas is absorbed, and then the slurry is pumped through the metering pump into the high-pressure reaction section for reaction. The high-pressure reaction section includes the reaction Pipes and mixers installed on the reaction pipes;
[0048] C. The slurry reacted in the high-pressure reaction section enters the pressure relief discharge section, which includes a pressure relief valve, a buffer tank, a condenser, an acidification kettle, and a filter press which are connected in sequence. The pressure valve enters the buffer tank afte...
Embodiment 2
[0050] A high-pressure continuous reaction system for the production of 3,6-dichlorosalicylic acid, comprising a batching tank 1, a carbon dioxide absorption tank 2, a high-pressure reaction section, and a pressure-relief discharging section connected in sequence; the high-pressure reaction section includes a reaction The pipeline 3 and the mixer 4 arranged on the reaction pipeline 3, the pressure relief discharging section includes a pressure relief valve 5, a buffer tank 6, a condenser 7, an acidification kettle 8 and a filter press 9 connected in sequence.
[0051] The batching tank 1 is connected to the carbon dioxide absorption tank 2 through a metering pump, the carbon dioxide absorption tank 2 is connected to the high-pressure reaction section through a metering pump, and the high-pressure reaction section is connected to the pressure relief valve 5 through the The buffer tank 6 is connected, the buffer tank 6 is connected to one end of the condenser 7, the other end of the...
Embodiment 3
[0060] On the basis of Example 1:
[0061] Preferably, in step A, the preparation process of the potassium 2,5-dichlorophenol is: under the protection of nitrogen, dissolving 2,5-dichlorophenol in xylene to obtain 2,5-dichlorophenol The xylene solution of phenol, and then the potassium hydroxide aqueous solution was added dropwise to the xylene solution of 2,5-dichlorophenol under stirring. After the dropwise addition is completed, heat to boiling, distill, and measure the moisture content of the distilled xylene to reach At 200ppm, stop the distillation, and then lower the temperature to 20°C to obtain potassium 2,5-dichlorophenolate solution.
[0062] Preferably, in step A, carbon dioxide gas is introduced into the batching kettle for protection after batching.
[0063] Preferably, in step A, the mass ratio of the potassium 2,5-dichlorophenate, xylene, anhydrous potassium carbonate powder, and dispersant is 1:4:0.5:0.01.
[0064] Furthermore, the dispersant is one or a mixture of t...
PUM
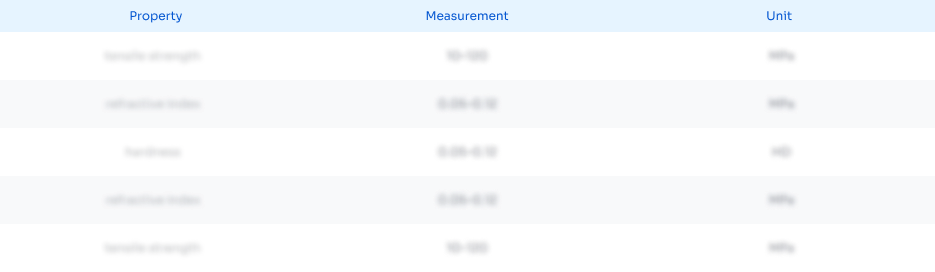
Abstract
Description
Claims
Application Information

- R&D
- Intellectual Property
- Life Sciences
- Materials
- Tech Scout
- Unparalleled Data Quality
- Higher Quality Content
- 60% Fewer Hallucinations
Browse by: Latest US Patents, China's latest patents, Technical Efficacy Thesaurus, Application Domain, Technology Topic, Popular Technical Reports.
© 2025 PatSnap. All rights reserved.Legal|Privacy policy|Modern Slavery Act Transparency Statement|Sitemap|About US| Contact US: help@patsnap.com