Multi-stage control device and method for dynamic tension of optical fiber winding machine
A technology of a control device and a control method, applied in the field of optical fiber winding, can solve the problems of inability to quickly and accurately control the optical fiber tension, inability to accurately adjust the optical fiber tension, single change of the speed of the pay-off wheel, etc. Powerful effect
- Summary
- Abstract
- Description
- Claims
- Application Information
AI Technical Summary
Problems solved by technology
Method used
Image
Examples
Embodiment Construction
[0030] Preferred embodiments of the present invention will be described in detail below in conjunction with the accompanying drawings.
[0031] refer to figure 1 , the preferred embodiment of the present invention provides a multi-stage dynamic tension control device for optical fiber winding machine, including a pay-off wheel 1 and a take-up ring 6, and also includes a guide wheel A4 and a guide wheel B5, the pay-off wheel 1, the guide wheel A4, the guide wheel B5 is fixedly arranged successively from left to right, and the take-up ring can be movably arranged at the right end, and a tensioning wheel 7 that can move up and down is arranged between the guiding wheel A4 and the guiding wheel B5, and the tensioning wheel 7 The lower part is fixedly connected with a pull pressure sensor 8 and a micro-motion mechanism 9 in turn, and the micro-motion mechanism 9 can make the tension wheel 7 and the pull pressure sensor 8 move up and down at the same time, and the pay-off wheel 1 is...
PUM
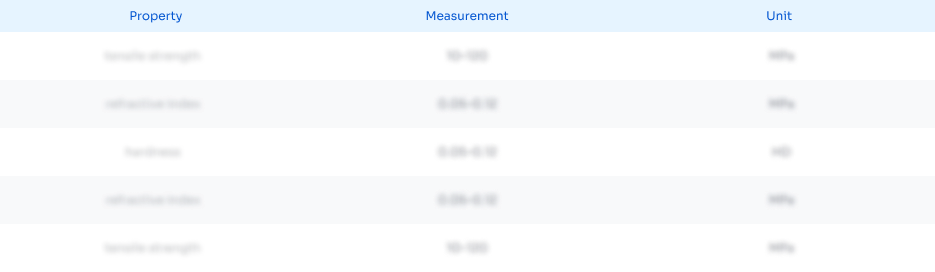
Abstract
Description
Claims
Application Information

- Generate Ideas
- Intellectual Property
- Life Sciences
- Materials
- Tech Scout
- Unparalleled Data Quality
- Higher Quality Content
- 60% Fewer Hallucinations
Browse by: Latest US Patents, China's latest patents, Technical Efficacy Thesaurus, Application Domain, Technology Topic, Popular Technical Reports.
© 2025 PatSnap. All rights reserved.Legal|Privacy policy|Modern Slavery Act Transparency Statement|Sitemap|About US| Contact US: help@patsnap.com