Ultrasonic measurement system, kinematic mechanism and method for operating an ultrasonic transmitter-receiver
A receiving device, ultrasonic measurement technology, applied in the direction of measuring device, radio wave measurement system, sound wave re-radiation, etc., can solve the problems of detection robustness limit, limited measurement update rate, low anti-interference, etc.
- Summary
- Abstract
- Description
- Claims
- Application Information
AI Technical Summary
Problems solved by technology
Method used
Image
Examples
Embodiment Construction
[0029] figure 1 A schematic top view of an exemplary embodiment of an ultrasonic measuring system 20 according to the invention with ultrasonic sensors 1 , 2 , 3 , 4 , 5 , 6 in the bumper of a car 10 as kinematics is shown. . The ultrasound sensors 1 , 2 , 3 , 4 , 5 , 6 have corresponding transmission lobes 11 , 12 , 13 , 14 , 15 , 16 . The ultrasonic sensors 1 , 2 , 3 , 4 , 5 , 6 are respectively connected via signal lines to a central control unit 7 as an analysis and processing unit. Depending on the surrounding objects, the ultrasonic sensors 1 , 2 , 3 , 4 , 5 , 6 are only capable of receiving cross-echoes from each other only conditionally. By way of example, the ultrasonic sensors 1 , 2 , 3 , 4 , 5 , 6 are divided into groups G12 , G23 , G34 , G45 , G56 in order to be able to take into account the possibility or impossibility of cross echoes. For example, groups G12 and G45 are arranged so far apart from one another that an echo based on the signal of group G45 cannot...
PUM
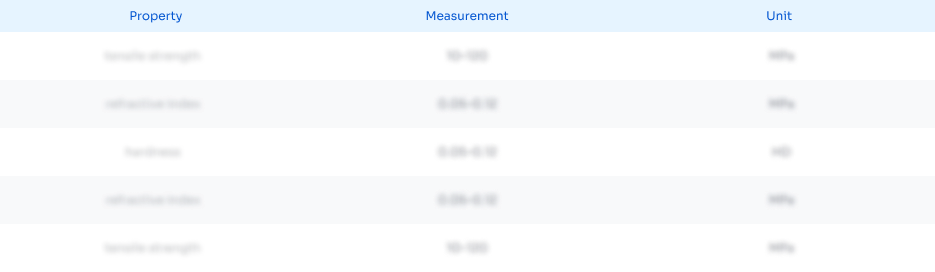
Abstract
Description
Claims
Application Information

- R&D Engineer
- R&D Manager
- IP Professional
- Industry Leading Data Capabilities
- Powerful AI technology
- Patent DNA Extraction
Browse by: Latest US Patents, China's latest patents, Technical Efficacy Thesaurus, Application Domain, Technology Topic, Popular Technical Reports.
© 2024 PatSnap. All rights reserved.Legal|Privacy policy|Modern Slavery Act Transparency Statement|Sitemap|About US| Contact US: help@patsnap.com