Preparation method for heavy oil catalytic cracking catalyst
A technology for cracking catalysts and heavy oil catalysis, which is applied in catalytic cracking, physical/chemical process catalysts, molecular sieve catalysts, etc. It can solve the problems of small pore volume in catalysts, poor cracking ability of heavy oil, and easy clogging of substrates, etc., and achieve low cost of raw materials , prolong service life, good effect
- Summary
- Abstract
- Description
- Claims
- Application Information
AI Technical Summary
Problems solved by technology
Method used
Examples
Embodiment 1
[0048] Add 1140 grams of deionized water, 2078 grams of kaolin, 1656 grams of pseudoboehmite, 2174 grams of aluminum sol in the reaction kettle, add 230 grams of hydrochloric acid with a concentration of 35% after 10 minutes of beating, the pH value is 0.7, and stir for 1 hour Then add 116 grams of ammonia water, after mixing evenly, the pH value is 4.8, aging for 12 hours, stirring for 30 minutes, then adding 2060 grams of REUSY molecular sieves, 123 grams of ZSM-5 and Mix slurry composed of 2388 grams of deionized water, beating for 30 minutes, spray dry, and roast the obtained catalyst microspheres at 500°C for 0.5 hours, then add 8 times of deionized water, stir evenly, wash at 80°C for 15 minutes, filter and dry That is, the FCC catalyst prepared by the method of the present invention is obtained, which is denoted as A1.
[0049] Catalyst A1 has an attrition index of 1.7 and a pore volume of 0.40 mL.g -1 , Microreactive 81.
Embodiment 2
[0051] Add 2262 grams of deionized water, 1656 grams of pseudoboehmite, 2174 grams of aluminum sol, 1078 grams of montmorillonite, 968 grams of modified montmorillonite (montmorillonite roasted at 650 ° C for 2 hours) in the reaction kettle, and beat After 10 minutes, add 200 grams of hydrochloric acid with a concentration of 35%, and the pH value is 1.3. After stirring for 30 minutes, add 98 grams of alkaline silica sol. Colloid milling until 1937 grams of REUSY molecular sieve with an average particle size of less than 5 microns, 123 grams of ZSM-5 molecular sieve and 3510 grams of deionized water mixed molecular sieve slurry, after beating for 30 minutes, spray drying, and the obtained catalyst microspheres at 500 ° C Roast for 0.5 hours, then add 8 times of deionized water, stir evenly, wash at 80°C for 15 minutes, filter and dry to obtain the FCC catalyst prepared by the method of the present invention, and record it as A2.
[0052] The wear index of catalyst A2 is 1.5, t...
Embodiment 3
[0070] Add 700 grams of deionized water, 2174 grams of aluminum sol, 1280 grams of kaolin and 550 grams of halloysite in the reaction kettle, add 200 grams of hydrochloric acid with a concentration of 25% after beating for 10 minutes, mix well and add 1904 grams under stirring Pseudo-boehmite, the pH value after homogenization is 1.2, after stirring for 2 hours, add 98 grams of sodium metaaluminate, the pH value after mixing is 4.3, aging for 10 hours, stirring for 30 minutes, adding self-use colloid mill and grinding to 1860 grams of REUSY molecular sieve with an average particle size of less than 5 microns, 100 grams of ZSM-5 and 2905 grams of deionized water mixed molecular sieve slurry, spray-dried after 30 minutes of beating, the obtained catalyst microspheres were roasted at 500 ° C for 0.5 hours, and then added 8 times deionized water, stirred evenly, washed at 80°C for 15 minutes, filtered and dried to obtain the FCC catalyst prepared by the method of the present invent...
PUM
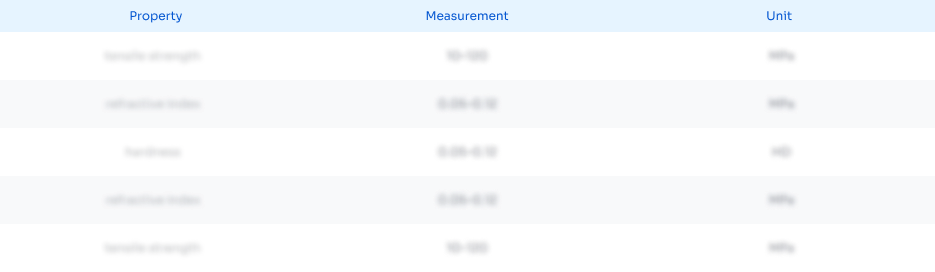
Abstract
Description
Claims
Application Information

- R&D
- Intellectual Property
- Life Sciences
- Materials
- Tech Scout
- Unparalleled Data Quality
- Higher Quality Content
- 60% Fewer Hallucinations
Browse by: Latest US Patents, China's latest patents, Technical Efficacy Thesaurus, Application Domain, Technology Topic, Popular Technical Reports.
© 2025 PatSnap. All rights reserved.Legal|Privacy policy|Modern Slavery Act Transparency Statement|Sitemap|About US| Contact US: help@patsnap.com