Injection molding device with spherical rotor
An injection molding device and spherical rotor technology, applied in the field of injection molding devices, can solve the problems of inconvenient barrel cleaning, large axial temperature difference, screw plasticization, crushing and extrusion capabilities, etc., and achieve simple and reliable structure, extrusion strong pressure effect
- Summary
- Abstract
- Description
- Claims
- Application Information
AI Technical Summary
Problems solved by technology
Method used
Image
Examples
Embodiment 1
[0032] Such as Figure 1 to Figure 3 As shown, it is an injection molding device with a spherical rotor, including an injection cylinder 1, an injection seat frame 2, a motor 3, a transmission mechanism 4, a seat 5, a centripetal thrust bearing 6, a hopper 7, a barrel 8, a plastic Chemical rotor 9, electric heater 10, vibrating device 11, motion controller 12, mobile oil cylinder 13, gear 14 and plunger 15;
[0033] The injection cylinder 1 , motor 3 , transmission mechanism 4 and barrel 8 are fixed on the injection seat frame 2 .
[0034] The barrel 8 includes a hemispherical plasticizing cavity 81 and an injection cylinder 82, and the hopper 7 is installed on the plasticizing cavity 81 of the barrel 8;
[0035] Described plasticizing rotor 9 comprises hemispherical rotor 91 and the cylindrical body 92 that is integrated with hemispherical rotor 91, is provided with continuous external screw groove 911 on described hemispherical rotor 91, and hemispherical rotor 91 and cylin...
Embodiment 2
[0043] Such as Figure 4 As shown, it is an injection molding device with a spherical rotor. Its basic mechanism principle is basically the same as that of Embodiment 1. The difference is that the inner hole of the injection cylinder 82 is a stepped hole, and the part with a large diameter in the stepped hole is related to the plasticizing Cavity 81 is connected, and the part of the small hole in the stepped hole is connected with the injection hole. There is a certain gap between the outer circular surface of the right part of the plunger 15 and the section with a large hole in the stepped hole, and the plasticized melt can be injected under pressure. Enter the right section of the injection cylinder 82 through this gap, and the outer circular surface of the right part of the plunger 15 is in a sliding fit with the part with a small diameter in the stepped hole, but the molten material cannot pass through the fitting gap, and the part with a small diameter in the stepped hole ...
Embodiment 3
[0045] Such as Figure 5 As shown, it is an injection molding device with a spherical rotor. Its structure and working principle are basically the same as those in Embodiment 1. The reverse head 16 , the one-way valve or the check head 16 is located in the injection cylinder 82 , and the one-way valve or the check head 11 can move axially in the injection cylinder 82 .
[0046] When working, the motor 3 drives the hemispherical rotor 91 to rotate through the transmission mechanism 4 and the gear 14. The external thread groove 911 on the hemispherical rotor 91 and the plasticizing cavity 81 of the machine barrel 8 form a material plasticizing and transporting channel. The material enters the external thread groove 911 on the outer circumference of the hemispherical rotor 91 through the radial hole of the plasticizing chamber 81 of the barrel 8, moves to the right side along the external thread groove 911 to the right end of the hemispherical rotor 91 and enters the injection ba...
PUM
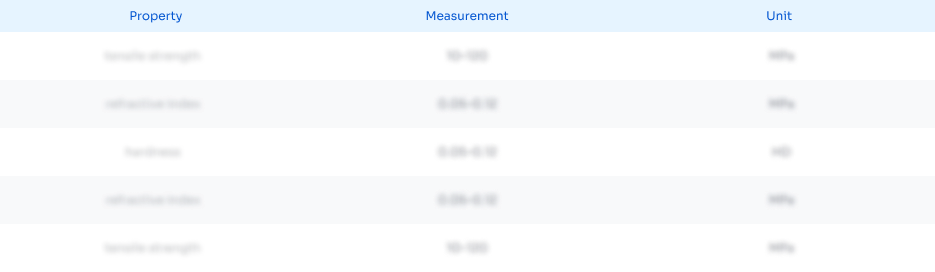
Abstract
Description
Claims
Application Information

- R&D
- Intellectual Property
- Life Sciences
- Materials
- Tech Scout
- Unparalleled Data Quality
- Higher Quality Content
- 60% Fewer Hallucinations
Browse by: Latest US Patents, China's latest patents, Technical Efficacy Thesaurus, Application Domain, Technology Topic, Popular Technical Reports.
© 2025 PatSnap. All rights reserved.Legal|Privacy policy|Modern Slavery Act Transparency Statement|Sitemap|About US| Contact US: help@patsnap.com