Molding method of automotive interior part with multilayered structure
A molding method and technology for automotive interiors, applied in household components, household appliances, other household appliances, etc., can solve the problems of complex processes, uneven skin texture, breakdown, etc., and achieve uniform surface texture and good appearance. Effect
- Summary
- Abstract
- Description
- Claims
- Application Information
AI Technical Summary
Problems solved by technology
Method used
Examples
Embodiment 1
[0022] The manipulator grabs the TPO skin with a buffer layer and moves it to the first heating device. The temperature of the second heating device on the manipulator is set at 60°C, and the temperature of the first heating device is set at 120°C. When the TPO skin with a buffer layer When heated to 120°C, the manipulator moves the softened skin into the cavity of the die. The mold is closed, the vacuum equipment on the cavity side is started, the skin is adsorbed to the surface of the mold cavity, the booster equipment on the side of the mold core is opened, the skin is completely attached to the surface of the mold cavity, and the preliminary skin texture is completed copy. Then the mold is slightly opened by 1mm, the molten polypropylene resin is injected into the mold cavity, the mold is closed, and the molten PP resin is pressed onto the TPO skin with a buffer layer, and the skin is further pressed against the mold skin after being subjected to the pressure of injection ...
Embodiment 2
[0024] The manipulator grabs the TPO skin and moves to the first heating device. The temperature of the second heating device on the manipulator is set at 100°C, and the set temperature of the first heating device is 100°C. When the TPO skin is heated to 110°C, the manipulator The softened skin is moved and placed in the cavity of the die. The mold is closed, the vacuum equipment on the cavity side is started, the skin is adsorbed to the surface of the mold cavity, the booster equipment on the side of the mold core is opened, the skin is completely attached to the surface of the mold cavity, and the preliminary skin texture is completed copy. Then the mold is slightly opened by 5mm, the molten ABS resin is injected into the mold cavity, the mold is closed, and the molten ABS resin is pressed onto the TPO skin with a buffer layer, and the skin is further pressed to the mold skin after being subjected to the pressure of injection and holding pressure After cooling, the resin an...
Embodiment 3
[0026] The manipulator grabs the PV°C skin and moves to the first heating device. The second heating device on the manipulator is turned off. The temperature of the first heating device is set at 150°C. When the TPO skin is heated to 150°C, the manipulator will soften the The skin is moved and placed in the cavity of the die. The mold is closed, the vacuum equipment on the cavity side is started, the skin is adsorbed to the surface of the mold cavity, the booster equipment on the side of the mold core is opened, the skin is completely attached to the surface of the mold cavity, and the preliminary skin texture is completed copy. The molten PP resin is injected into the mold cavity, and the skin is further pressed to the textured surface of the mold by the pressure of injection and holding pressure to obtain a better textured effect. After cooling, the resin and the skin are combined to form a multi-layer structure interior parts.
PUM
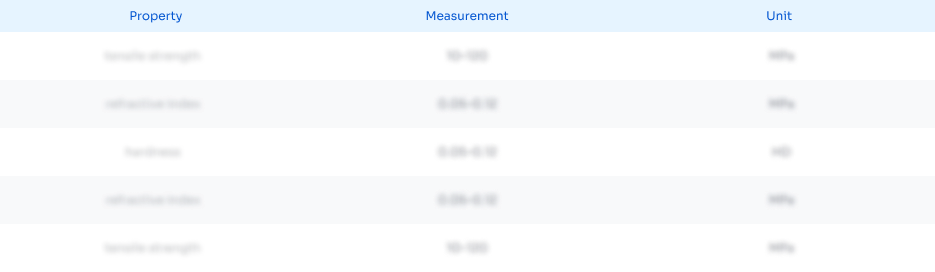
Abstract
Description
Claims
Application Information

- R&D
- Intellectual Property
- Life Sciences
- Materials
- Tech Scout
- Unparalleled Data Quality
- Higher Quality Content
- 60% Fewer Hallucinations
Browse by: Latest US Patents, China's latest patents, Technical Efficacy Thesaurus, Application Domain, Technology Topic, Popular Technical Reports.
© 2025 PatSnap. All rights reserved.Legal|Privacy policy|Modern Slavery Act Transparency Statement|Sitemap|About US| Contact US: help@patsnap.com