A method and system for removing heavy hydrocarbons from natural gas
A technology for natural gas and heavy hydrocarbons, applied in the field of liquefied natural gas production, can solve the problems of increased process complexity, poor separation effect, large energy consumption, etc., to improve resource utilization efficiency, increase process added value, and reduce unit energy consumption. Effect
- Summary
- Abstract
- Description
- Claims
- Application Information
AI Technical Summary
Problems solved by technology
Method used
Image
Examples
Embodiment 1
[0037] For the specific process flow of this embodiment, please refer to figure 1 .
[0038] A system for removing heavy hydrocarbons from natural gas, comprising: a first flow path A1 of a cold box 1, a second flow path A2, a third flow path A3, a demethanizer 2, a deethanizer 3, and a demethanizer condensation 4, deethanizer reboiler 5, heavy hydrocarbon cooler 6, first valve V1 to fourth valve V4 and corresponding connecting pipelines, wherein demethanizer 2 and deethanizer 3 are packed towers, and There are two sections of packing. The inlet of the first channel A1 of the cold box 1 is connected to the raw gas pipeline, and the outlet is connected to the feed port at the bottom of the demethanizer 2 through the first valve, and the feed port is located below the packing of the demethanizer 2; The inlet of the second channel A2 is connected to the shell-side gas phase outlet of the demethanizer condenser 4, and the outlet is connected to the LNG product pipeline; the inle...
Embodiment 2
[0041] For the specific process flow of this embodiment, please refer to figure 1 .
[0042] The raw natural gas I from the outside is passed into the inlet of the first channel A1 of the cold box 1. The raw natural gas is natural gas that has been deacidified, dehydrated, demercurized, and rich in heavy hydrocarbons, with a flow rate of 1265kg / h and a pressure of 6.5MPa , the temperature is -30°C, the total content of heavy hydrocarbons is 40ppmv, of which the content of neopentane is 10ppmv, the content of benzene is 10ppmv, and the content of C6 and above hydrocarbons is 20ppmv. After being cooled by the first channel A1 of the cold box 1, the temperature drops to - Natural gas II in a gas-liquid two-phase state is obtained at 80°C. The natural gas II is decompressed to 6MPa through the first valve V1 and then enters the bottom feed port of the demethanizer 2. After being purified by heavy hydrocarbon removal rectification, the temperature at the bottom of the tower is -82 ...
Embodiment 3
[0044] For the specific process flow of this embodiment, please refer to figure 1 .
[0045] The raw natural gas I from the outside is passed into the inlet of the first channel A1 of the cold box 1. The raw natural gas is natural gas that has been deacidified, dehydrated, demercurized, and rich in heavy hydrocarbons, with a flow rate of 14570kg / h and a pressure of 3.5MPa , the temperature is 35°C, the total content of heavy hydrocarbons is 10000ppmv, of which the content of neopentane is 400ppmv, the content of benzene is 600ppmv, and the content of C6 and above hydrocarbons is 9000ppmv. After being cooled by the first channel A1 of the cold box 1, the temperature drops to -45 ℃ to obtain natural gas II in a gas-liquid two-phase state. The natural gas II is decompressed to 3.4MPa through the first valve V1 and then enters the bottom feed port of the demethanizer 2. After heavy hydrocarbon removal and rectification purification, the temperature at the bottom of the tower is -4...
PUM
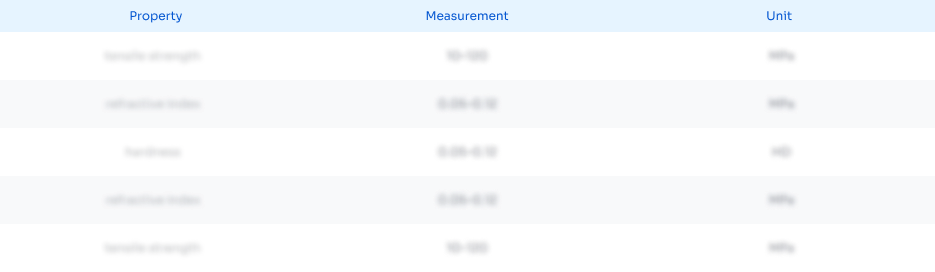
Abstract
Description
Claims
Application Information

- R&D Engineer
- R&D Manager
- IP Professional
- Industry Leading Data Capabilities
- Powerful AI technology
- Patent DNA Extraction
Browse by: Latest US Patents, China's latest patents, Technical Efficacy Thesaurus, Application Domain, Technology Topic, Popular Technical Reports.
© 2024 PatSnap. All rights reserved.Legal|Privacy policy|Modern Slavery Act Transparency Statement|Sitemap|About US| Contact US: help@patsnap.com