Pumpback type friction stir welding head based on parallel mechanism
A friction stir welding and friction stir technology, which is used in welding equipment, non-electric welding equipment, metal processing equipment, etc., can solve the problems of complex product structure and welding seam form, slow response speed of series mechanism, and large error transmission. High torque and high bearing capacity, easy kinematic decoupling calculation, and the effect of ensuring surface integrity
- Summary
- Abstract
- Description
- Claims
- Application Information
AI Technical Summary
Problems solved by technology
Method used
Image
Examples
Embodiment Construction
[0020] The invention will be described in more detail hereinafter with reference to the accompanying drawings showing embodiments of the invention. However, this invention may be embodied in many different forms and should not be construed as limited to the embodiments set forth herein.
[0021] Such as figure 1 As shown, the retractable friction stir welding head based on the parallel mechanism provided by the preferred embodiment of the present invention includes: the rear mounting seat 1 of the friction stir welding head, the drive assembly 2 of the PRS mechanism, the front mounting plate 3 of the friction stir welding head, and the ball Lead screw subassembly 4, linear moving plate 5, hinge plate 6, Hooke hinge assembly 7, parallel head-spindle installation moving platform 8, retractable electric spindle 9.
[0022] The rear mounting base 1 of the friction stir welding machine head is installed with the Z-axis sliding plate through screws, so as to realize the connection ...
PUM
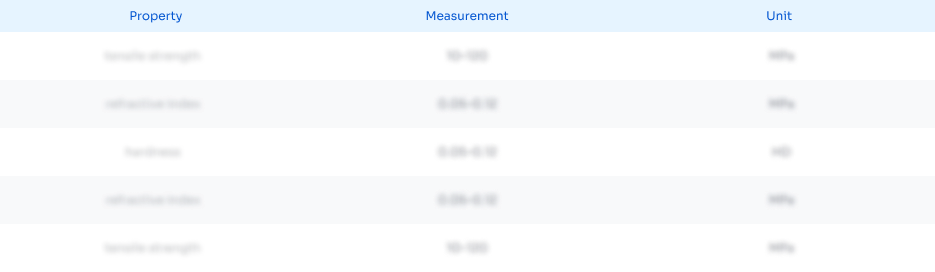
Abstract
Description
Claims
Application Information

- Generate Ideas
- Intellectual Property
- Life Sciences
- Materials
- Tech Scout
- Unparalleled Data Quality
- Higher Quality Content
- 60% Fewer Hallucinations
Browse by: Latest US Patents, China's latest patents, Technical Efficacy Thesaurus, Application Domain, Technology Topic, Popular Technical Reports.
© 2025 PatSnap. All rights reserved.Legal|Privacy policy|Modern Slavery Act Transparency Statement|Sitemap|About US| Contact US: help@patsnap.com