Photocatalytic oxidation and molecular sieve absorption catalytic oxidation method for industrial waste gas VOCs
A photocatalytic oxidation, industrial waste gas technology, applied in separation methods, chemical instruments and methods, gas treatment, etc., can solve problems such as increased equipment operating costs, high ozone concentration, VOCs and ozone molecules escape.
- Summary
- Abstract
- Description
- Claims
- Application Information
AI Technical Summary
Problems solved by technology
Method used
Examples
example 1
[0032] An Electronics Co., Ltd. in Nantong, Jiangsu Province, drying and forming section, with an exhaust air volume of 8000m 3 / h, pretreated by wet spray adsorption device (scrubbing tower), and then subjected to a catalytic oxidation, molecular sieve adsorption, and a second catalytic oxidation. TiO2 is used as a catalyst in the first catalytic oxidation and the second catalytic oxidation. Total non-methane hydrocarbons are 28mg / m 3 、39mg / m 3 , 22mg / m 3 、31mg / m 3 (120mg / m 3 , GB16297-1996); the average detection value of O3 (ozone) 4 times in 1 hour is 63ug / m 3 、41ug / m 3 、32ug / m 3 、69ug / m 3 (200ug / m 3 , GB3095-2012).
example 2
[0034] A Shandong Chemical Co., Ltd. has an extraction production section with an exhaust air volume of 12000m3 / h. It is pretreated by a wet spray adsorption device (scrubber), and then undergoes a catalytic oxidation, molecular sieve adsorption, and a second catalytic oxidation. The first catalytic oxidation and the second 55% TiO is used in catalytic oxidation 2 and 45% MnO 2 Composite catalyst, 3 detections of formaldehyde in the exhaust gas are 8mg / m 3 、19mg / m 3 , 12mg / m 3 (25mg / m 3 , GB16297-1996); O 3 (Ozone) The average detection value of 4 times in 1 hour is 65ug / m 3 、48ug / m 3 、35ug / m 3 、79ug / m 3 (200ug / m 3 , GB3095-2012).
example 3
[0036] A Shanghai Resin Co., Ltd., drying molding section, exhaust air volume 12000m 3 / h, pretreated by a wet spray adsorption device (scrubbing tower), and then subjected to a catalytic oxidation, molecular sieve adsorption, and a second catalytic oxidation. The first catalytic oxidation and the second catalytic oxidation use 80% TiO 2 and 20% MnO2 Composite catalyst, non-methane total hydrocarbons in the exhaust gas detected 3 times are 17mg / m 3 、29mg / m 3 , 26mg / m 3 , 21mg / m 3 (120mg / m 3 , GB16297-1996); O 3 (Ozone) The average detection value of 4 times in 1 hour is 65ug / m 3 、48ug / m 3 、35ug / m 3 、79ug / m 3 (200ug / m 3 , GB3095-2012).
PUM
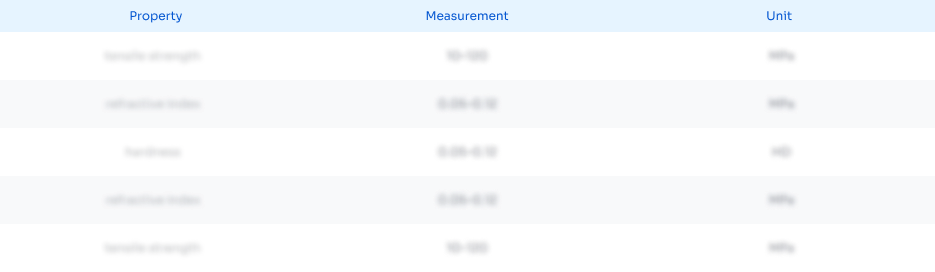
Abstract
Description
Claims
Application Information

- Generate Ideas
- Intellectual Property
- Life Sciences
- Materials
- Tech Scout
- Unparalleled Data Quality
- Higher Quality Content
- 60% Fewer Hallucinations
Browse by: Latest US Patents, China's latest patents, Technical Efficacy Thesaurus, Application Domain, Technology Topic, Popular Technical Reports.
© 2025 PatSnap. All rights reserved.Legal|Privacy policy|Modern Slavery Act Transparency Statement|Sitemap|About US| Contact US: help@patsnap.com