A modified polyphenylene oxide material with low dielectric loss and a preparing method thereof
A polyphenylene ether, modification technology, applied in the field of low dielectric loss modified polyphenylene ether material and its preparation, can solve the problems of large dielectric loss, etc., to achieve increased fluidity, easy processing, and good electrical properties Effect
- Summary
- Abstract
- Description
- Claims
- Application Information
AI Technical Summary
Problems solved by technology
Method used
Image
Examples
Embodiment 1
[0022] (1) Take each component raw material by the following parts by weight:
[0023]
[0024] (2) The above raw materials are mixed at high speed by a high-speed mixer, the speed of the high-mixer is 800-1000rmp, the mixing temperature is 40°C, and mixed for 10 minutes; the mixed material is passed through a twin-screw extruder, and the temperature of each zone is controlled at 260- At 290°C, the strands were cut into pellets to obtain modified polyphenylene ether materials.
Embodiment 2
[0026] (1) Take each component raw material by the following parts by weight:
[0027]
[0028] (2) Mix the above raw materials at a high speed with a high-speed mixer, control the speed of the high-mixer to 800-1000rmp, mix the temperature at 60°C, and mix for 3 minutes; pass the mixed material through a twin-screw extruder, and control the temperature of each zone at 240-1000rmp At 275°C, the extruder strands were cut into pellets to obtain modified polyphenylene ether materials.
Embodiment 3
[0030] (1) Take each component raw material by the following parts by weight:
[0031]
[0032] (2) The above raw materials are mixed at high speed by a high-speed mixer, the speed of the high-mixer is 800-1000rmp, the mixing temperature is 50°C, and mixed for 6 minutes; the mixed material is passed through a twin-screw extruder, and the temperature of each zone is controlled at 250- At 280°C, the strands were cut into pellets to obtain modified polyphenylene ether materials.
PUM
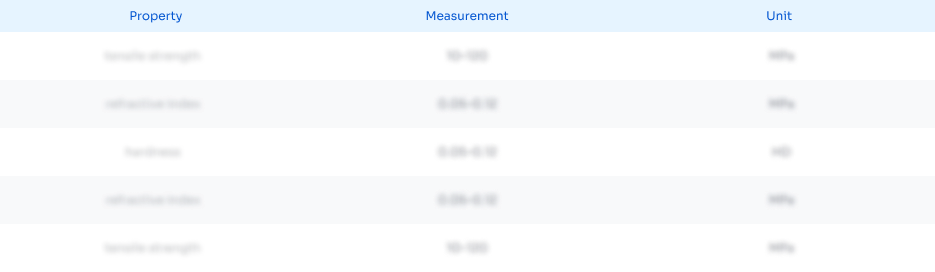
Abstract
Description
Claims
Application Information

- Generate Ideas
- Intellectual Property
- Life Sciences
- Materials
- Tech Scout
- Unparalleled Data Quality
- Higher Quality Content
- 60% Fewer Hallucinations
Browse by: Latest US Patents, China's latest patents, Technical Efficacy Thesaurus, Application Domain, Technology Topic, Popular Technical Reports.
© 2025 PatSnap. All rights reserved.Legal|Privacy policy|Modern Slavery Act Transparency Statement|Sitemap|About US| Contact US: help@patsnap.com