Automatic ignition control system and method for hot blast stove
An automatic ignition and control system technology, applied in furnaces, blast furnaces, heating furnaces, etc., can solve the problems of increasing the labor intensity of operators, damage to the structure of the combustion chamber of the hot blast stove, and heat loss of the hot blast stove, and achieve stable automatic ignition control, The effect of reducing labor intensity and preventing deflagration
- Summary
- Abstract
- Description
- Claims
- Application Information
AI Technical Summary
Problems solved by technology
Method used
Image
Examples
Embodiment Construction
[0028] The present invention will be further described below in conjunction with the embodiments and accompanying drawings.
[0029] refer to figure 1 As shown, the automatic ignition control system of the hot blast stove according to the present invention includes an air ramp setter, an air flow signal selector, an air flow regulator, a gas ramp setter, a gas flow signal selector, and a gas flow regulator The air ramp setter and the gas ramp setter both include 6 input ports and 1 output port (each port of the air ramp setter and the gas ramp setter is realized by programming the PLC controller), 6 The input ports are: start signal (Boolean quantity) input terminal, second pulse signal input terminal, flow setting value input terminal, ramp time input terminal, flow upper limit setting value input terminal, reset signal input terminal (Boolean quantity), 1 output port is the flow given value output port;
[0030] The start signal input terminal and flow given value output t...
PUM
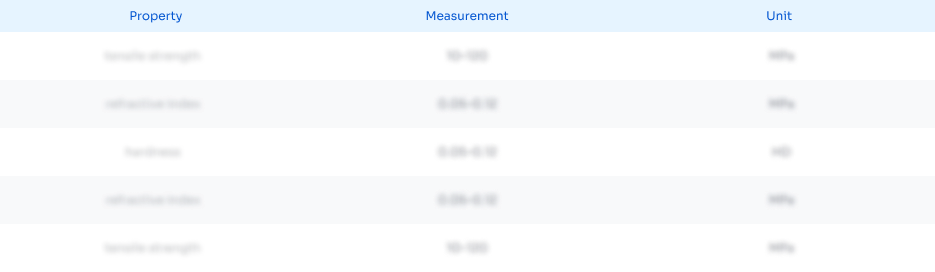
Abstract
Description
Claims
Application Information

- R&D
- Intellectual Property
- Life Sciences
- Materials
- Tech Scout
- Unparalleled Data Quality
- Higher Quality Content
- 60% Fewer Hallucinations
Browse by: Latest US Patents, China's latest patents, Technical Efficacy Thesaurus, Application Domain, Technology Topic, Popular Technical Reports.
© 2025 PatSnap. All rights reserved.Legal|Privacy policy|Modern Slavery Act Transparency Statement|Sitemap|About US| Contact US: help@patsnap.com