A secondary annealing process for polysilicon ingot
A secondary annealing and polysilicon technology, applied in crystal growth, post-processing details, post-processing, etc., to achieve the effects of improving mechanical properties, saving production costs, and increasing the number of pieces produced
- Summary
- Abstract
- Description
- Claims
- Application Information
AI Technical Summary
Problems solved by technology
Method used
Examples
Embodiment 1
[0014] Embodiment 1, a kind of secondary annealing process of polysilicon ingot, its steps are as follows:
[0015] (1) The silicon raw material is annealed for the first time after the heating, melting and crystal growth process in the ingot casting process. The annealing temperature is 1330°C and the temperature is kept for 1h;
[0016] (2) Lower the temperature of the silicon ingots after the first annealing by reducing the heating power and closing the heat shield, and then perform the second annealing.
Embodiment 2
[0017] Embodiment 2, a kind of secondary annealing process of polysilicon ingot, its steps are as follows:
[0018] (1) The silicon raw material is annealed for the first time after the heating, melting, and crystal growth processes in the ingot casting process. The annealing temperature is 1380 ° C and the temperature is kept for 2.5 hours;
[0019] (2) Lower the temperature of the silicon ingot after the first annealing by reducing the heating power and closing the heat shield, and then perform the second annealing.
Embodiment 3
[0020] Embodiment 3, a kind of secondary annealing process of polysilicon ingot, its steps are as follows:
[0021] (1) The silicon raw material is annealed for the first time after the heating, melting, and crystal growth processes in the ingot casting process. The annealing temperature is 1350 ° C and the temperature is kept for 2 hours;
[0022] (2) Lower the temperature of the silicon ingot after the first annealing by reducing the heating power and closing the heat shield, and then perform the second annealing, the annealing temperature is 1200 ° C, keep it for 1 hour, and then proceed to the subsequent process.
PUM
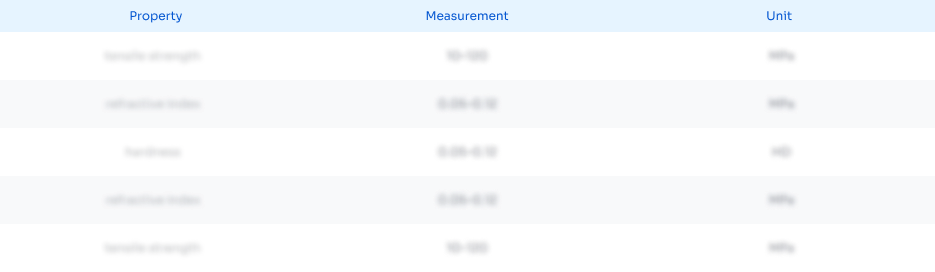
Abstract
Description
Claims
Application Information

- R&D
- Intellectual Property
- Life Sciences
- Materials
- Tech Scout
- Unparalleled Data Quality
- Higher Quality Content
- 60% Fewer Hallucinations
Browse by: Latest US Patents, China's latest patents, Technical Efficacy Thesaurus, Application Domain, Technology Topic, Popular Technical Reports.
© 2025 PatSnap. All rights reserved.Legal|Privacy policy|Modern Slavery Act Transparency Statement|Sitemap|About US| Contact US: help@patsnap.com