Roll-to-roll continuous grapheme film growth device and technique
A graphene film, roll-to-roll technology, applied in metal material coating process, gaseous chemical plating, coating and other directions, can solve the problem of difficult to adapt to high-speed and large-scale growth, graphene tearing and wrinkling, and inability to achieve large-scale Problems such as rapid preparation of area graphene
- Summary
- Abstract
- Description
- Claims
- Application Information
AI Technical Summary
Problems solved by technology
Method used
Image
Examples
Embodiment 1
[0015] A rapid cooling plasma-enhanced CVD roll-to-roll continuous growth furnace production process, which includes an organism, characterized in that: the body is provided with a workbench, and the two ends of the workbench are respectively provided with a vacuum chamber a and a vacuum chamber b , the vacuum chamber a and the vacuum chamber b are connected with a vacuum unit, the vacuum chamber a is provided with an air inlet, and the vacuum chamber b at the other end is provided with an air outlet, the vacuum chamber Both the chamber a and the vacuum chamber b are provided with an unwinding drum, and a rotating motor is arranged on the unwinding drum at the same time, a vacuum tube is connected between the vacuum chamber a and the vacuum chamber b, and the vacuum chamber a One side is equipped with a radio frequency plasma generator, a heating furnace, and a liquid nitrogen cold trap in sequence.
[0016] A roll-to-roll continuous graphene film production process, the speci...
Embodiment 2
[0022] A roll-to-roll continuous graphene film production process, the specific production steps are as follows:
[0023] 1) Put the coiled copper foil on the discharge roller in the vacuum chamber a, and connect it to the discharge roller in the vacuum chamber b through the vacuum tube, and close the hatch of the feeding and air intake chamber;
[0024] 2) Put the coiled copper-nickel alloy roll (85% copper, 15% nickel) on the discharge roller in the feed inlet cavity, and pass through the furnace tube to connect with the winding roller in the discharge exhaust cavity. Close the hatch of the feed intake cavity, turn on the vacuum unit, and pump the air pressure in the entire equipment to below 0.3Pa. Turn on the heating furnace body, raise the temperature in the furnace to the growth temperature of 1030°C, then inject hydrogen gas at a flow rate of 50 SCCM, turn on the radio frequency plasma generator and adjust the radio frequency power to 300 watts. Start the motor connect...
Embodiment 3
[0027] A roll-to-roll continuous graphene film growth process, comprising the following steps:
[0028] 1) Put the coiled copper foil on the discharge roller in the vacuum chamber a, and connect it to the discharge roller in the vacuum chamber b through the vacuum tube, and close the hatch of the feeding and air intake chamber;
[0029] 2) Put the roll-shaped nickel foil into the discharge roller in the feed intake chamber, and pass through the furnace tube to connect with the winding roller in the discharge exhaust chamber. Close the hatch of the feed intake cavity, turn on the vacuum unit, and pump the air pressure in the entire equipment to below 0.3Pa. Turn on the heating furnace body, increase the temperature in the furnace to the growth temperature of 500°C, then inject hydrogen gas at a flow rate of 50 SCCM, turn on the radio frequency plasma generator and adjust the radio frequency power to 300 watts. Start the motor connected to the take-up roller. Then the copper f...
PUM
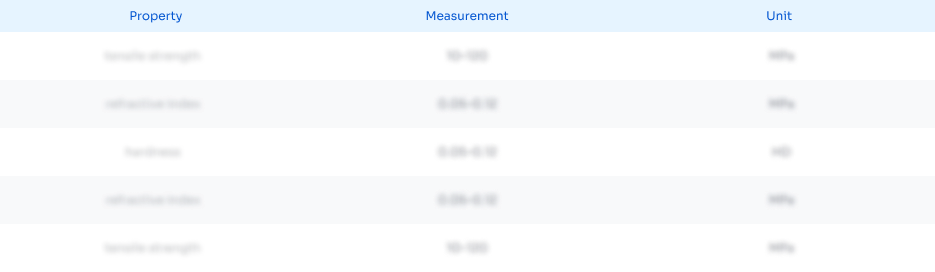
Abstract
Description
Claims
Application Information

- R&D
- Intellectual Property
- Life Sciences
- Materials
- Tech Scout
- Unparalleled Data Quality
- Higher Quality Content
- 60% Fewer Hallucinations
Browse by: Latest US Patents, China's latest patents, Technical Efficacy Thesaurus, Application Domain, Technology Topic, Popular Technical Reports.
© 2025 PatSnap. All rights reserved.Legal|Privacy policy|Modern Slavery Act Transparency Statement|Sitemap|About US| Contact US: help@patsnap.com