Method for preparing high-purity graphite fluoride according to catalytic method
A fluorinated graphite, high-purity technology, applied in the field of high-purity fluorinated graphite prepared by catalytic method, can solve problems such as injury, increased production cost, equipment corrosion and personal safety, and achieve low production cost, high safety, and reduced production cost Effect
- Summary
- Abstract
- Description
- Claims
- Application Information
AI Technical Summary
Problems solved by technology
Method used
Image
Examples
Embodiment 1
[0045] Get flake graphite 1kg, aluminum fluoride 0.2kg and put into reactor 2 after mixing uniformly. Nitrogen gas was introduced and the temperature was raised to 120° C., and the volatile impurities were removed at constant temperature for 1 hour. The reactor 2 was heated to 300°C, and 10% by volume of fluorine gas was introduced to react. The pressure in the reactor 2 was normal pressure. After 12 hours of reaction, the heating was stopped, and nitrogen gas was introduced into the reactor 2 for replacement. After the temperature in the reactor 2 is lowered to normal temperature, the product is taken out, directly added to deionized water for stirring, and the graphite fluoride is separated from the aluminum fluoride doped therein. Fish out the floating graphite fluoride, and repeat this process until no precipitation occurs. The aluminum fluoride submerged in water is washed and dried and reused as a catalyst. The obtained fluorinated graphite was dispersed in 10% hydrofl...
Embodiment 2
[0047] Get ultrafine graphite 2kg, magnesium fluoride 0.5kg and put into reactor 2 after mixing uniformly. Introduce argon gas and raise the temperature to 150° C., and keep the temperature for 3 hours to remove volatile impurities therein. The reactor 2 was heated to 350°C, and 35% by volume of fluorine gas was introduced to react. The pressure in the reactor 2 was 0.5 MPa. After 15 hours of reaction, the heating was stopped, and nitrogen gas was introduced into the reactor 2 for replacement. After the temperature in the reactor 2 is lowered to normal temperature, the product is taken out and directly added to deionized water for stirring, so that the graphite fluoride is separated from the magnesium fluoride doped therein. Fish out the floating graphite fluoride, and repeat this process until no precipitation occurs. The magnesium fluoride submerged in water is washed and dried and used as a catalyst repeatedly. The obtained fluorinated graphite was dispersed in 15% hydrof...
Embodiment 3
[0049]Get 3kg of colloidal graphite and 1kg of calcium fluoride and mix them uniformly and put them into reactor 2. Nitrogen gas was introduced and the temperature was raised to 150° C., and the volatile impurities were removed at constant temperature for 3 hours. The reactor 2 was heated up to 400°C, and fluorine gas with a volume percentage of 40% was introduced to react. The pressure in the reactor 2 was 1.0 MPa. After 15 hours of reaction, the heating was stopped, and argon gas was introduced into the reactor 2 for replacement. After the temperature in the reactor 2 drops to normal temperature, the product is taken out, and directly added to deionized water for stirring, so that the graphite fluoride is separated from the calcium fluoride doped therein. Fish out the floating graphite fluoride, and repeat this process until no precipitation occurs. The calcium fluoride sunken into the water is washed and dried and reused as a catalyst. The obtained fluorinated graphite wa...
PUM
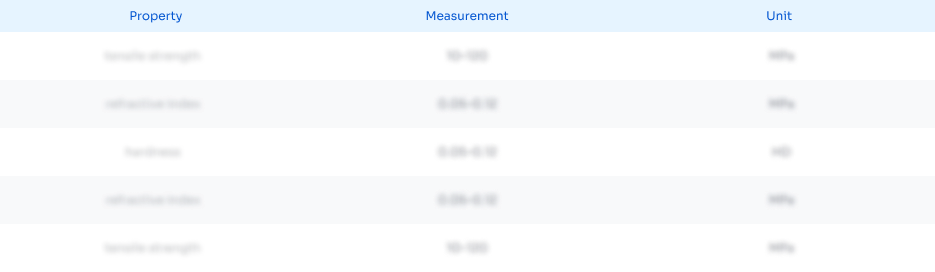
Abstract
Description
Claims
Application Information

- Generate Ideas
- Intellectual Property
- Life Sciences
- Materials
- Tech Scout
- Unparalleled Data Quality
- Higher Quality Content
- 60% Fewer Hallucinations
Browse by: Latest US Patents, China's latest patents, Technical Efficacy Thesaurus, Application Domain, Technology Topic, Popular Technical Reports.
© 2025 PatSnap. All rights reserved.Legal|Privacy policy|Modern Slavery Act Transparency Statement|Sitemap|About US| Contact US: help@patsnap.com