Powder material compression molding method assisted by ultrasonic vibration
A powder material, press molding technology, applied in material molding presses, presses, manufacturing tools, etc., can solve the problems of uneven density distribution inside the compact, inconsistent effective pressure, pressure loss, etc., to achieve high quality Forming preparation, increasing effective pressure, increasing the effect of densification
- Summary
- Abstract
- Description
- Claims
- Application Information
AI Technical Summary
Problems solved by technology
Method used
Image
Examples
Embodiment 1
[0031] figure 1 It is a schematic structural diagram of the safety equipment for pressing and molding powder materials assisted by ultrasonic vibration provided in Embodiment 1 of the present invention. Such as figure 1 As shown, the equipment includes an ultrasonic base 1 , an ultrasonic die set 2 installed on the ultrasonic base 1 , an ultrasonic punch 3 used in conjunction with the ultrasonic die set 2 , and a hydraulic press for driving the ultrasonic punch 3 .
[0032] In this example, if figure 2 As shown, the ultrasonic die set 2 includes a cover plate 21 , eyebolts 22 , a powder pressing chamber 23 , a lower die 24 , and a circulating water cooling system. The circulating water cooling system includes a water pipe 25 , a liquid inlet 251 and a liquid outlet 252 . Eyebolts 22 are provided on the cover plate 21 and the lower die 24 . The joint between the powder pressing chamber 23 and the cover plate 21, the joint between the powder pressing chamber 23 and the liqui...
Embodiment 2
[0041] Embodiment 2 provides a powder material compression molding method assisted by ultrasonic vibration, which includes the following steps.
[0042] Step (1): Place the powder material to be pressed in the ultrasonic mold sleeve, between the ultrasonic punch and the ultrasonic base.
[0043] Step (2): Start the cooling water circulation system, the coolant is injected from the liquid inlet of the cooling water circulation system and flows out from the liquid outlet.
[0044] Step (2) Specifically, inject coolant into the liquid inlet of the ultrasonic mold sleeve and the liquid inlet of the ultrasonic punch, so that the coolant is injected from the liquid inlet of the cooling water circulation system and flows out from the liquid outlet, thereby starting the ultrasonic mold sleeve. The cooling water circulation system and the cooling water circulation system in the ultrasonic punch.
[0045] Step (3): Start the hydraulic press, and the ultrasonic punch makes relative moti...
PUM
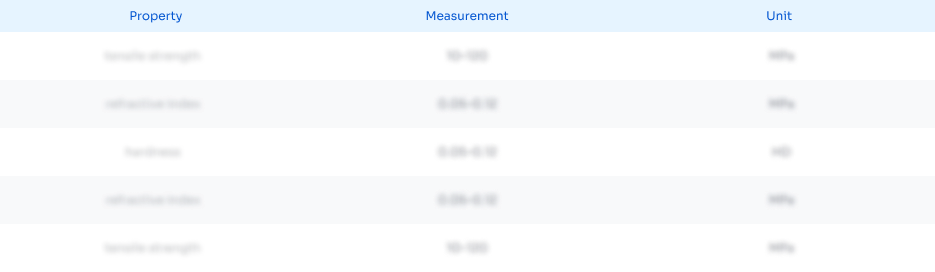
Abstract
Description
Claims
Application Information

- R&D
- Intellectual Property
- Life Sciences
- Materials
- Tech Scout
- Unparalleled Data Quality
- Higher Quality Content
- 60% Fewer Hallucinations
Browse by: Latest US Patents, China's latest patents, Technical Efficacy Thesaurus, Application Domain, Technology Topic, Popular Technical Reports.
© 2025 PatSnap. All rights reserved.Legal|Privacy policy|Modern Slavery Act Transparency Statement|Sitemap|About US| Contact US: help@patsnap.com