A Welding Fixture for a Passenger Car Cabin Door Frame
A technology for welding fixtures and skeletons, applied in welding equipment, auxiliary welding equipment, welding/cutting auxiliary equipment, etc., can solve the problems of lowering the quality of the hatch door skeleton, occupying more space for fixtures, increasing input costs, etc., and shortening production. The effect of cycle, wide range of use and convenient welding
- Summary
- Abstract
- Description
- Claims
- Application Information
AI Technical Summary
Problems solved by technology
Method used
Image
Examples
Embodiment
[0028] Such as Figure 1-5 As shown, a welding fixture for the cabin door frame of a passenger car includes a BASE plate 1 and a movable positioning unit, the movable positioning unit is installed on the BASE plate 1, and the BASE plate includes a channel steel chassis 11 and a steel plate 12, the present Embodiment adopts 10# channel steel and 2040 * 1336 * 16mm thick steel plate, described steel plate 12 is placed on channel steel chassis 11, it is characterized in that, described steel plate 12 is provided with linear slide rail, and described movable The positioning unit slides on the linear slide rail. The movable positioning unit includes the first type of movable positioning unit 2, the second type of movable positioning unit 3 and the third type of movable positioning unit 4. For different skeleton weldments, by replacing different The type of movable positioning unit can quickly build a suitable welding fixture.
[0029] Such as image 3 As shown, the first type of ...
PUM
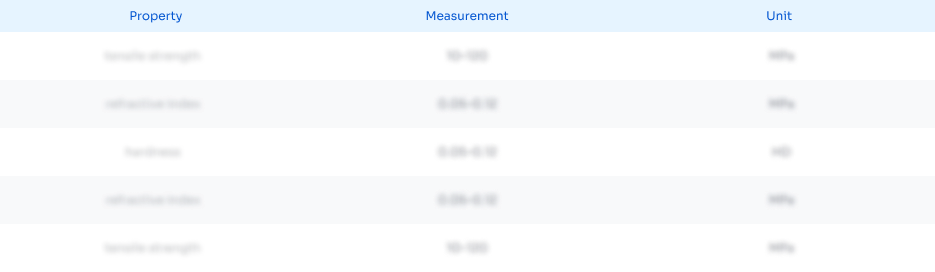
Abstract
Description
Claims
Application Information

- Generate Ideas
- Intellectual Property
- Life Sciences
- Materials
- Tech Scout
- Unparalleled Data Quality
- Higher Quality Content
- 60% Fewer Hallucinations
Browse by: Latest US Patents, China's latest patents, Technical Efficacy Thesaurus, Application Domain, Technology Topic, Popular Technical Reports.
© 2025 PatSnap. All rights reserved.Legal|Privacy policy|Modern Slavery Act Transparency Statement|Sitemap|About US| Contact US: help@patsnap.com