Device applying pulsed TIG electric arc for assisting MIG welding and welding method achieved by adopting device
An arc and pulse technology, applied in arc welding equipment, welding equipment, manufacturing tools, etc., can solve problems such as poor stability, and achieve the effects of improving stability, simple structure, and reducing welding spatter
- Summary
- Abstract
- Description
- Claims
- Application Information
AI Technical Summary
Problems solved by technology
Method used
Image
Examples
specific Embodiment approach 1
[0040] Specific embodiment one: see figure 1 with figure 2 To explain this embodiment, a device that uses pulsed TIG arc assisted MIG welding described in this embodiment includes a MIG welding power source 1, a TIG welding power source 2, a MIG welding gun 3, a TIG welding gun 4, an IGBT switch control system 5 and an IGBT Switch 6;
[0041] The MIG welding torch 3’s fuser electrode clamp is used to clamp the fuser welding wire, and the TIG welding torch 4’s tungsten electrode clamp is used to clamp the tungsten electrode.
[0042] The positive output terminal of the MIG welding power source 1 is connected to the fusion electrode clamp of the MIG welding torch 3, and the negative output terminal of the MIG welding power source 1 is connected to one end of the workpiece to be welded.
[0043] The negative output terminal of the TIG welding power source 2 is connected to the other end of the workpiece to be welded, the positive output terminal of the TIG welding power source 2 is con...
specific Embodiment approach 2
[0045] Embodiment 2: The difference between this embodiment and the device for assisting MIG welding using pulsed TIG arc as described in the first embodiment is that the MIG welding power source 1 is a constant voltage MIG welding power source, and the TIG welding power source 2 is Constant current TIG welding power source.
specific Embodiment approach 3
[0046] Embodiment 3: The difference between this embodiment and the device for applying pulsed TIG arc-assisted MIG welding described in the first embodiment is that it also includes two four-degree-of-freedom clamping mechanisms, and the two four The degree of freedom clamping mechanism is used to clamp the MIG welding torch 3 and the TIG welding torch 4, and each four-degree-of-freedom clamping mechanism is used to realize translational movement along the x-axis, y-axis and z-axis and rotation around the y-axis .
[0047] In this embodiment, two four-degree-of-freedom clamping mechanisms are included, and the two four-degree-of-freedom clamping mechanisms are used to clamp the MIG welding torch 3 and the TIG welding torch 4, each of which is used for It realizes translational movement along the x-axis, y-axis and z-axis and rotation around the y-axis, which improves the automation level of welding, and improves welding efficiency and welding accuracy.
PUM
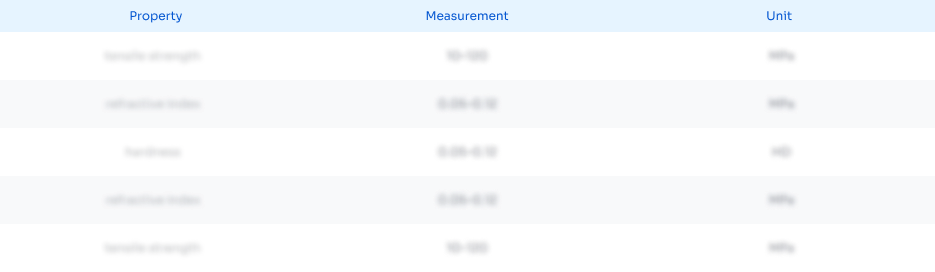
Abstract
Description
Claims
Application Information

- Generate Ideas
- Intellectual Property
- Life Sciences
- Materials
- Tech Scout
- Unparalleled Data Quality
- Higher Quality Content
- 60% Fewer Hallucinations
Browse by: Latest US Patents, China's latest patents, Technical Efficacy Thesaurus, Application Domain, Technology Topic, Popular Technical Reports.
© 2025 PatSnap. All rights reserved.Legal|Privacy policy|Modern Slavery Act Transparency Statement|Sitemap|About US| Contact US: help@patsnap.com