Composite enzyme preparation for degumming of linen fiber raw material, preparation method of composite enzyme preparation and degumming method of linen fiber raw material
A compound enzyme preparation and flax fiber technology, which is applied in the chemical post-treatment of fibers, plant raw materials, fiber treatment, etc., can solve the problems of low enzyme activity, instability, and damage to the breaking strength of flax fibers, and achieve an increase in elongation at break , The effect of increasing the breaking strength and reducing the production cost
- Summary
- Abstract
- Description
- Claims
- Application Information
AI Technical Summary
Problems solved by technology
Method used
Image
Examples
preparation example Construction
[0086] Applicant also proposed a kind of preparation method for the compound enzyme preparation of flax fiber raw material degumming, it is characterized in that, comprises the following steps:
[0087] Step (1): Pretreating the raw material enzyme preparation alkaline pectate lyase, alkaline cellulase, alkaline xylanase and laccase respectively;
[0088] Step (2): mixing 70% of alkaline pectate lyase, 2% of alkaline cellulase, 18% of alkaline xylanase and 10% of laccase in a mixer;
[0089] Step (3): Then add an appropriate amount of preservative and sterilize through a diatomaceous earth filter, and then measure the enzyme activity to prepare a compound enzyme preparation for degumming flax fiber raw materials.
Embodiment 1
[0091] A production test was carried out in a factory in Jiaxing, Zhejiang. The specific formula of the compound enzyme preparation was as follows, and the mass percentages were: alkaline pectate lyase 70%, alkaline cellulase 2%, alkaline xylanase 18%, lacquer Enzymes 10%.
[0092] The raw enzyme preparations are pretreated respectively, and then mixed uniformly in a mixer according to the proportion, then an appropriate amount of preservative is added, and the bacteria are sterilized through a diatomaceous earth filter, and then the enzyme activity is measured and quantitatively packaged to become a product.
[0093] From June 30th to July 29th, 2015, a total of 30 days, 3 tons of flax worsted yarn were produced every day. Each pot of scouring pot can process 1 ton of raw material fiber, add 1200 grams of enzyme, the amount of enzyme added is 1.2‰, the process conditions of compound enzyme action: action temperature: 55 °C; pH value: 7.5; action time: 2h; stirring: circulatio...
Embodiment 2
[0097] A production test was carried out in a factory in Taizhou, Jiangsu. The specific formula of the compound enzyme preparation is as follows, and the mass percentages are: alkaline pectate lyase 70%, alkaline cellulase 2%, alkaline xylanase 18%, laccase 10% %.
[0098] The raw enzyme preparations are pretreated respectively, and then mixed uniformly in a mixer according to the proportion, then an appropriate amount of preservative is added, and the bacteria are sterilized through a diatomaceous earth filter, and then the enzyme activity is measured and quantitatively packaged to become a product.
[0099] From November 7th to December 2nd, 2015, a total of 26 days, 2.5 tons of flax worsted yarn were produced every day. Each pot of scouring pot can process 1 ton of raw material fiber, add 1500 grams of enzyme, the amount of enzyme added is 1.5‰, the process conditions of compound enzyme action: action temperature: 50 °C; pH value: 8.0; action time: 3h Stirring: circulating ...
PUM
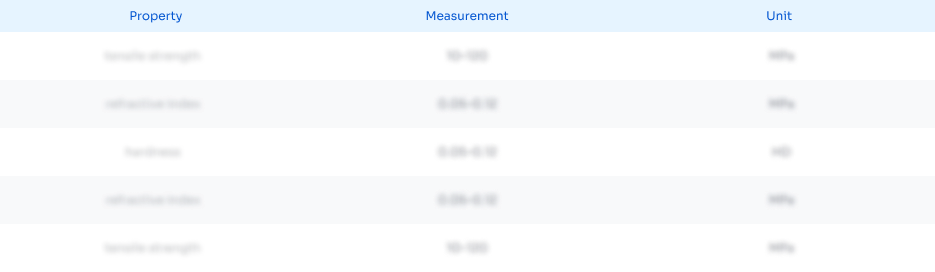
Abstract
Description
Claims
Application Information

- Generate Ideas
- Intellectual Property
- Life Sciences
- Materials
- Tech Scout
- Unparalleled Data Quality
- Higher Quality Content
- 60% Fewer Hallucinations
Browse by: Latest US Patents, China's latest patents, Technical Efficacy Thesaurus, Application Domain, Technology Topic, Popular Technical Reports.
© 2025 PatSnap. All rights reserved.Legal|Privacy policy|Modern Slavery Act Transparency Statement|Sitemap|About US| Contact US: help@patsnap.com