Flue gas waste heat utilization system for annealing furnace
A flue gas waste heat and annealing furnace technology, which is applied to furnaces, furnace materials, waste heat treatment, etc., can solve the problems of increasing the load of induced draft fans, wasting flue gas heat energy, and wasting heat energy, so as to reduce the exhaust gas temperature, prevent environmental pollution, and improve The effect of the recycling effect
- Summary
- Abstract
- Description
- Claims
- Application Information
AI Technical Summary
Problems solved by technology
Method used
Image
Examples
Embodiment Construction
[0010] Below in conjunction with accompanying drawing and specific embodiment the present invention will be described in further detail: figure 1 As shown, the annealing furnace flue gas waste heat utilization system includes an annealing furnace 1, a heat exchanger 2 connected with the annealing furnace 1, a flue 21 and an exhaust chimney 22, and the heat exchanger 2 is provided with a dust removal function Air intake part 11, a cooling furnace 4 is arranged between the chimney 22 and the heat exchanger 2, a water spray pump 32 is connected above the cooling furnace 4, and a water tank 3 is connected to the water spray pump 32. The cooling furnace 4, a cooling water cooling device 44 is connected below, and a filtering device 43 is arranged between the cooling furnace 4 and the cooling water cooling device 44. The cooling water cooling device 44 is also connected with a water pump 45, and the water pump 45 The cooled water in the cooling water cooling device 44 is input into ...
PUM
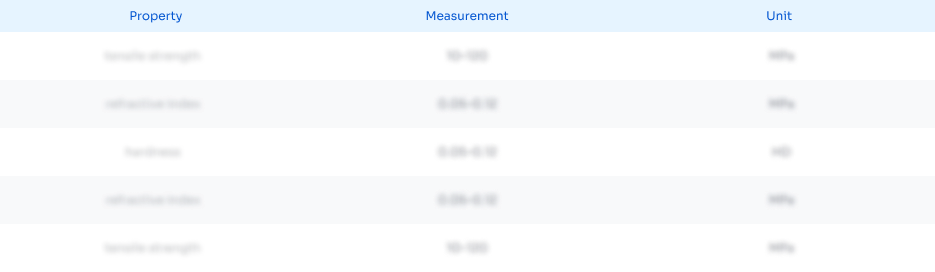
Abstract
Description
Claims
Application Information

- Generate Ideas
- Intellectual Property
- Life Sciences
- Materials
- Tech Scout
- Unparalleled Data Quality
- Higher Quality Content
- 60% Fewer Hallucinations
Browse by: Latest US Patents, China's latest patents, Technical Efficacy Thesaurus, Application Domain, Technology Topic, Popular Technical Reports.
© 2025 PatSnap. All rights reserved.Legal|Privacy policy|Modern Slavery Act Transparency Statement|Sitemap|About US| Contact US: help@patsnap.com