Electrochemical regeneration treatment method for waste lubricating oil
A waste lubricating oil and treatment method technology, applied in the direction of lubricating compositions, etc., can solve the problems of large chroma, low utilization rate of waste lubricating raw materials, unfavorable production operations, etc.
- Summary
- Abstract
- Description
- Claims
- Application Information
AI Technical Summary
Problems solved by technology
Method used
Examples
Embodiment 1
[0018] Select corresponding waste lubricating oil, through adopting conventional method to measure, the content of phosphorus in the waste lubricating oil is 4000ppm, then, directly waste lubricating oil and tetrahydrofuran methanol are added in the reactor in proportion, and reactor adopts conventional setting to get final product, reaction Preferably, the reactor can be separated into three regions by using a mesoporous membrane, so that graphite electrodes are placed in the regions on both sides of the reactor, which is conducive to more effective separation of the aggregates gathered on the electrodes, and the amount of tetrahydrofuran methanol solvent added is a waste 5.0% of the volume of the lubricating oil, then, the applied voltage is electrochemically treated to make the impurity particles gather around the electrode to form flocs, wherein, the voltage value of the applied voltage is 50V, and after the electrochemical treatment is completed, keep the energized state an...
Embodiment 2
[0020] Select corresponding waste lubricating oil, through adopting conventional method to measure, the content of phosphorus in the waste lubricating oil is 3500ppm, then, directly waste lubricating oil and tetrahydrofuran methanol are added in the reactor in proportion, and the reactor adopts conventional setting to get final product. A good reactor can be separated into three regions by using a mesoporous membrane, so that graphite electrodes can be placed in the regions on both sides of the reactor, which is conducive to more effective separation of aggregates gathered on the electrodes, so that the amount of tetrahydrofuran methanol solvent added is 10% of the volume of the waste lubricating oil, and then, the applied voltage is electrochemically treated to make the impurity particles gather around the electrode to form flocs, wherein the voltage value of the applied voltage is 80V, and after the electrochemical treatment is completed, keep the energized state, The liquid ...
Embodiment 3
[0022]Select corresponding waste lubricating oil, through adopting conventional method to measure, the content of phosphorus in the waste lubricating oil is 3800ppm, then, directly waste lubricating oil and tetrahydrofuran methanol are added in the reactor in proportion, and reactor adopts conventional setting to get final product, reaction Preferably, the reactor can be separated into three regions by using a mesoporous membrane, so that graphite electrodes can be placed in the regions on both sides of the reactor respectively, which is conducive to more effective separation of aggregates gathered on the electrodes, so that the addition of tetrahydrofuran methanol solvent is 4.0% of the volume of the waste lubricating oil, then, the applied voltage is electrochemically treated to make the impurity particles gather around the electrode to form flocs, wherein the voltage value of the applied voltage is 100V, and after the electrochemical treatment is finished, keep the energized ...
PUM
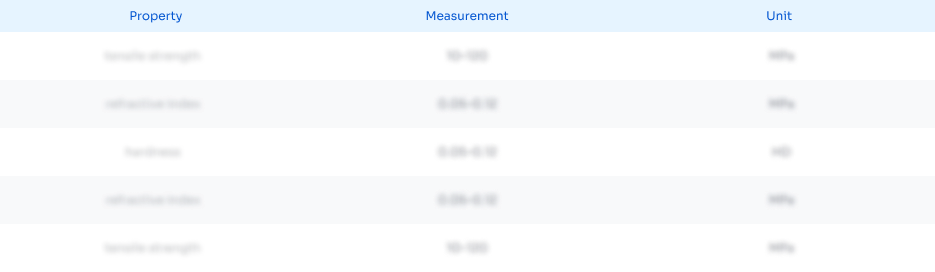
Abstract
Description
Claims
Application Information

- R&D Engineer
- R&D Manager
- IP Professional
- Industry Leading Data Capabilities
- Powerful AI technology
- Patent DNA Extraction
Browse by: Latest US Patents, China's latest patents, Technical Efficacy Thesaurus, Application Domain, Technology Topic, Popular Technical Reports.
© 2024 PatSnap. All rights reserved.Legal|Privacy policy|Modern Slavery Act Transparency Statement|Sitemap|About US| Contact US: help@patsnap.com