A kind of uv-led photocurable unsaturated polyester gel coat resin and coating preparation method thereof
A technology of polyester coating and gel coat resin, applied in the field of unsaturated polyester coating and its preparation, can solve the problems of poor acid and alkali resistance of unsaturated polyester, prone to orange peel, large shrinkage rate, etc. The effect of linking density, reducing volume shrinkage and improving coating rigidity
- Summary
- Abstract
- Description
- Claims
- Application Information
AI Technical Summary
Problems solved by technology
Method used
Image
Examples
Embodiment 1
[0038]Add 5.0g of triphenyl phosphite, 2.0g of sodium hypophosphite, 424.0g of diethylene glycol, 27.2g of pentaerythritol, and 355.6g of phthalic anhydride in sequence, and then add the electric stirring, water separator, thermometer, In the reaction vessel heated by the electric heating mantle, after heating to 100-110°C, start to stir slowly for half an hour, then raise the temperature to 160°C, react for 2 hours, cool down to 100°C and add 156.9g of maleic anhydride, the molar ratio of phthalic anhydride to maleic anhydride 3:2, react at constant temperature for 1 hour, raise the temperature to 195±2°C and react until the acid value is below 40mgKOH / g, add 0.5g hydroquinone, cool down to 95±1°C, slowly drop in 98.1g and mix in 0.6g Triphenyl phosphite, glycidyl methacrylate of 1.2g N,N'-dimethyl benzylamine is capped, and after the drop-in is completed, the temperature is slowly raised to 104±0.5°C, and the reaction is when the acid value is below 10mgKOH / g When the temper...
Embodiment 2
[0041] Put 5.0g of triphenyl phosphite, 2.0g of sodium hypophosphite, 381.6g of diethylene glycol, 36.8g of glycerol, and 370.0g of phthalic anhydride into the equipment equipped with electric stirring and water separator in sequence. , thermometer, electric heating mantle heating reaction vessel, after heating to 100-110°C, start to stir slowly for half an hour, then raise the temperature to 160°C, react for 2 hours, cool down to 100°C, add 98.0g maleic anhydride, phthalic anhydride and maleic anhydride The molar ratio is 2.5:1, react at constant temperature for 1 hour, raise the temperature to 195±2°C and react until the acid value is below 30mgKOH / g, add hydroquinone, cool down to 95±1°C, slowly drop in 74.3g and mix with 0.34 G triphenyl phosphite, 0.6g N, N-dimethyl phenylamine glycidyl methacrylate to end-capping, slowly warm up to 104±0.5°C after dropping, and react until the acid value is below 10mgKOH / g 286.0 g of styrene was added when the temperature dropped below 8...
Embodiment 3
[0044] Add 5.0g of triphenyl phosphite, 2.0g of sodium hypophosphite, 296.8g of diethylene glycol, 27.2g of pentaerythritol, and 370g of phthalic anhydride, and add them in sequence with electric stirring, water separator, thermometer, In the reaction vessel heated by the electric heating mantle, after heating to 100-110°C, start to stir slowly for half an hour, then raise the temperature to 160°C, react for 2 hours, cool down to 100°C and add 98g of maleic anhydride, the molar ratio of phthalic anhydride to maleic anhydride is 1:1, constant temperature reaction for 1 hour, heat up to 195±2°C and react until the acid value is below 90mgKOH / g, add hydroquinone, cool down to 95±1°C, slowly drop in 223.4g and mix with 0.6g triphosphite Phenyl ester, 1.2g of N,N'-dimethyl benyl amine glycidyl methacrylate for end-capping, after the drop-in is completed, the temperature is slowly raised to 104±0.5°C, and when the acid value is below 10mgKOH / g, the temperature is lowered When the te...
PUM
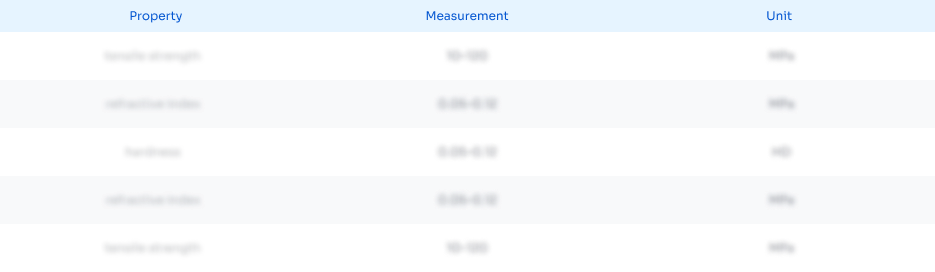
Abstract
Description
Claims
Application Information

- Generate Ideas
- Intellectual Property
- Life Sciences
- Materials
- Tech Scout
- Unparalleled Data Quality
- Higher Quality Content
- 60% Fewer Hallucinations
Browse by: Latest US Patents, China's latest patents, Technical Efficacy Thesaurus, Application Domain, Technology Topic, Popular Technical Reports.
© 2025 PatSnap. All rights reserved.Legal|Privacy policy|Modern Slavery Act Transparency Statement|Sitemap|About US| Contact US: help@patsnap.com