A shaping mold for making an insulating cylinder
A technology for shaping molds and insulating cylinders, which is used in the manufacture of insulators, insulators, inductors/transformers/magnets, etc., can solve the problems of high input cost, waste of materials, and cumbersome manufacturing process.
- Summary
- Abstract
- Description
- Claims
- Application Information
AI Technical Summary
Problems solved by technology
Method used
Image
Examples
Embodiment Construction
[0025] The present invention will be described in further detail below in conjunction with the accompanying drawings.
[0026] as attached Figure 9 As shown, the present invention is a sizing mold for making an insulating cylinder, which includes a first base plate 1, a second base plate 2, a third base plate 3 and a fourth base plate 4 sequentially connected to accommodate the heat-set The rectangular cylinder 5 of the insulating cylinder; the bottom of the rectangular cylinder 5 is provided with a holding device 10 for preventing the insulating cylinder to be heat-set from slipping out and for heat circulation; the holding device 10 is made of flat steel Build the welded well-shaped frame mechanism, wherein the well-shaped frame mechanism is welded with the first base plate 1, the second base plate 2, the third base plate 3 and the fourth base plate 4 to realize fixing on the bottom of the cylinder; The width of the cross-section of the inner cavity of the rectangular cyli...
PUM
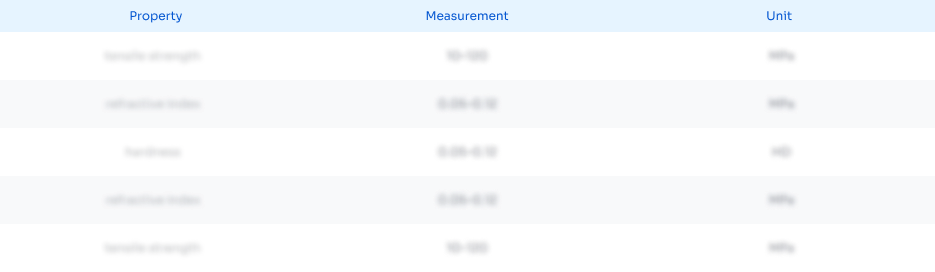
Abstract
Description
Claims
Application Information

- R&D
- Intellectual Property
- Life Sciences
- Materials
- Tech Scout
- Unparalleled Data Quality
- Higher Quality Content
- 60% Fewer Hallucinations
Browse by: Latest US Patents, China's latest patents, Technical Efficacy Thesaurus, Application Domain, Technology Topic, Popular Technical Reports.
© 2025 PatSnap. All rights reserved.Legal|Privacy policy|Modern Slavery Act Transparency Statement|Sitemap|About US| Contact US: help@patsnap.com