Tracking, correcting method of welding seam in cold rolling production line loop region and system thereof
A technology in the area and production line, applied in the direction of welding equipment, auxiliary welding equipment, welding/cutting auxiliary equipment, etc., can solve problems such as the inability to track the weld seam in the looper area, the failure of the weld detector to detect, and the large economic loss. Achieve the effect of reducing labor maintenance costs, improving labor productivity, and reducing unit parking
- Summary
- Abstract
- Description
- Claims
- Application Information
AI Technical Summary
Problems solved by technology
Method used
Image
Examples
Embodiment Construction
[0059] In order to make the objectives, technical solutions and advantages of the present invention clearer, the present invention will be described in further detail below in conjunction with the accompanying drawings and embodiments. It should be understood that the specific embodiments described here are only used to explain the present invention and are not intended to limit the invention.
[0060] Such as figure 1 As shown, the present invention provides a kind of tracking method of weld seam in looper area of cold rolling production line, and it comprises the following steps:
[0061] S1, calculate the strip theoretical length in the loop area by the absolute encoder 21 provided on the wire rope winch 20 connected with the looper trolley 10, and obtain the strip theoretical length curve in the loop area;
[0062] S2, through the incremental encoder 31 provided on the entrance tension roller 30, calculate the actual length of the strip steel that the weld seam enters i...
PUM
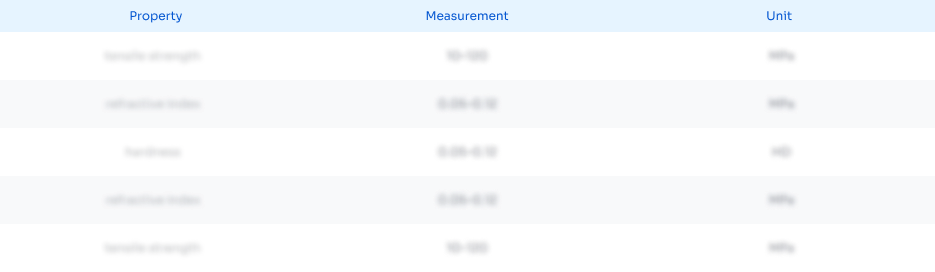
Abstract
Description
Claims
Application Information

- R&D
- Intellectual Property
- Life Sciences
- Materials
- Tech Scout
- Unparalleled Data Quality
- Higher Quality Content
- 60% Fewer Hallucinations
Browse by: Latest US Patents, China's latest patents, Technical Efficacy Thesaurus, Application Domain, Technology Topic, Popular Technical Reports.
© 2025 PatSnap. All rights reserved.Legal|Privacy policy|Modern Slavery Act Transparency Statement|Sitemap|About US| Contact US: help@patsnap.com