Shaft kiln burner and method
A technology of vertical kiln and mixing tube, which is applied in the combustion of refractory materials and in the field of vertical kiln burners. It can solve the problems of excess combustion gas, excess fuel, and insufficient combustion of gas, so as to reduce consumption, increase sintering speed, and improve sintering efficiency. quality effect
- Summary
- Abstract
- Description
- Claims
- Application Information
AI Technical Summary
Problems solved by technology
Method used
Image
Examples
Embodiment Construction
[0008] Such as figure 1 The specific embodiment of shaft kiln burner and method of the present invention shown is characterized in that an air pipe 1 is set, and an air intake pipe 3 is sleeved on the outside of the air pipe 1. There is a gap between the air intake pipe 3 and the air pipe 1, and the air intake pipe 1 3 The front end pipe wall is provided with a gas inlet 4, and the end of the intake pipe 3 close to the gas inlet 4 is provided with a plug 8, the outside of the intake pipe 3 is sleeved with a mixing pipe 2, and the rear wall of the mixing pipe 2 is provided with a gas port 13, The front end wall of the mixing tube 2 is provided with a gas mixing outlet 10, the conical surface of the mixing tube 2 is provided with a gas mixing outlet-a11, the front end wall of the mixing tube 2 is provided with a bracket 9, and the outside of the mixing tube 2 is equipped with a connecting plate 6, The secondary air pipe 14 is set outside the mixing pipe 2, the rear end of the se...
PUM
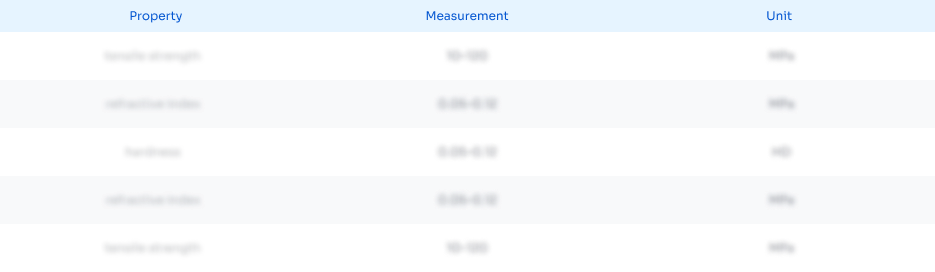
Abstract
Description
Claims
Application Information

- Generate Ideas
- Intellectual Property
- Life Sciences
- Materials
- Tech Scout
- Unparalleled Data Quality
- Higher Quality Content
- 60% Fewer Hallucinations
Browse by: Latest US Patents, China's latest patents, Technical Efficacy Thesaurus, Application Domain, Technology Topic, Popular Technical Reports.
© 2025 PatSnap. All rights reserved.Legal|Privacy policy|Modern Slavery Act Transparency Statement|Sitemap|About US| Contact US: help@patsnap.com