First-pass closed roll gap tail-swing rolling method for reversible cold rolling mill
A closed roll gap and cold rolling mill technology, which is applied in the field of the first pass closed roll gap tail flick rolling of reversible cold rolling mills, can solve the problem of slippage of the inner circle of the steel coil of the entrance coiler, the length of the unrolled strip tail of the rolling mill, Unstable rolling state and other problems can improve the surface quality, stabilize the tail rolling process, and improve the yield of finished products.
- Summary
- Abstract
- Description
- Claims
- Application Information
AI Technical Summary
Problems solved by technology
Method used
Image
Examples
Embodiment Construction
[0016] The embodiment of the first pass closed-gap drift rolling method of the reversing cold rolling mill according to the present invention will be described below with reference to the accompanying drawings. Those skilled in the art would recognize that the described embodiments can be modified in various ways or combinations thereof without departing from the spirit and scope of the invention. Accordingly, the drawings and description are illustrative in nature and not intended to limit the scope of the claims. Also, in this specification, the drawings are not drawn to scale, and like reference numerals denote like parts.
[0017] In this embodiment, a closed-gap drift rolling method for the first pass of a reversing cold rolling mill is provided, such as figure 1 As shown, it includes the following steps:
[0018] Step S102, before the first pass of closed roll gap tailing, control the pressure roll of the uncoiler, the pressure roll of the uncoil pinch roll, the pressu...
PUM
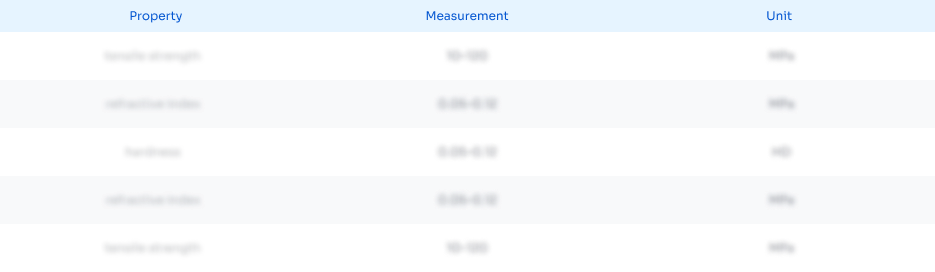
Abstract
Description
Claims
Application Information

- Generate Ideas
- Intellectual Property
- Life Sciences
- Materials
- Tech Scout
- Unparalleled Data Quality
- Higher Quality Content
- 60% Fewer Hallucinations
Browse by: Latest US Patents, China's latest patents, Technical Efficacy Thesaurus, Application Domain, Technology Topic, Popular Technical Reports.
© 2025 PatSnap. All rights reserved.Legal|Privacy policy|Modern Slavery Act Transparency Statement|Sitemap|About US| Contact US: help@patsnap.com