Method for manufacturing large curved-surface component of turbine
A turbine, curved surface technology used in the manufacture of large curved components for use in turbines
- Summary
- Abstract
- Description
- Claims
- Application Information
AI Technical Summary
Problems solved by technology
Method used
Image
Examples
Embodiment Construction
[0017] In order to make the purpose, technical solution and advantages of the present invention clearer, the following examples are given to further describe the present invention in detail.
[0018] figure 1 The flow chart of shows an embodiment of the method of the present invention, which relates to the method of manufacturing a large curved surface part for a turbine, comprising the following steps in sequence: Step S1 cutting a metal plate according to specific dimensions and according to the physical properties of said metal plate Selecting a hydraulic press; step S2 heating the metal plate to 400°C to 1200°C; step S3 putting the metal plate into a die and using the hydraulic press to maintain a pressure of 5MPa to 20MPa for 2 to 10 minutes to compress the metal The panels are molded into curved parts. When selecting a hydraulic press, those skilled in the art will understand that various physical properties such as the thickness, area, and weight of the metal plate sho...
PUM
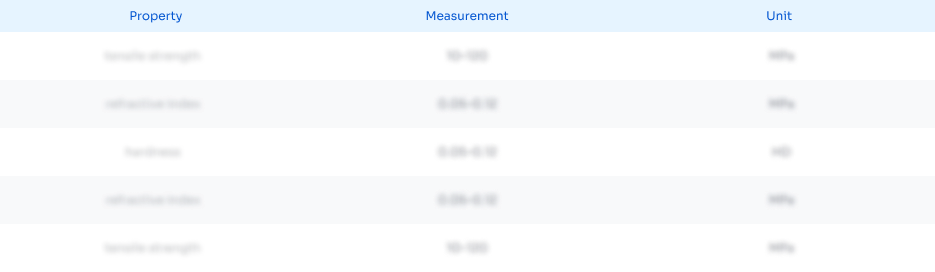
Abstract
Description
Claims
Application Information

- R&D
- Intellectual Property
- Life Sciences
- Materials
- Tech Scout
- Unparalleled Data Quality
- Higher Quality Content
- 60% Fewer Hallucinations
Browse by: Latest US Patents, China's latest patents, Technical Efficacy Thesaurus, Application Domain, Technology Topic, Popular Technical Reports.
© 2025 PatSnap. All rights reserved.Legal|Privacy policy|Modern Slavery Act Transparency Statement|Sitemap|About US| Contact US: help@patsnap.com