High reliability control method and high reliability control system in multi-robot system
A multi-robot and control method technology, applied in the direction of instruments, data processing applications, prediction, etc., can solve problems such as difficulty in satisfying robustness, complex and changeable multi-robot system organizational structure, and impossibility to implement robot fault-tolerant control, etc., to achieve The effect of dynamic control and cost reduction
- Summary
- Abstract
- Description
- Claims
- Application Information
AI Technical Summary
Problems solved by technology
Method used
Image
Examples
Embodiment Construction
[0045] The present invention will be described in detail below in conjunction with specific embodiments. The following examples will help those skilled in the art to further understand the present invention, but do not limit the present invention in any form. It should be noted that those skilled in the art can make several modifications and improvements without departing from the concept of the present invention. These all belong to the protection scope of the present invention.
[0046] The present invention is mainly a high-reliability control technology for multi-robot systems. Firstly, it proposes multi-robot system working group division and physical topology design for the controlled system, which is the root of high-reliability systems. After the robot has a physical structure, it needs to be controlled by a controller. Based on the above idea, the present invention proposes a high-reliability control method and system in a multi-robot system.
[0047] A high reliabi...
PUM
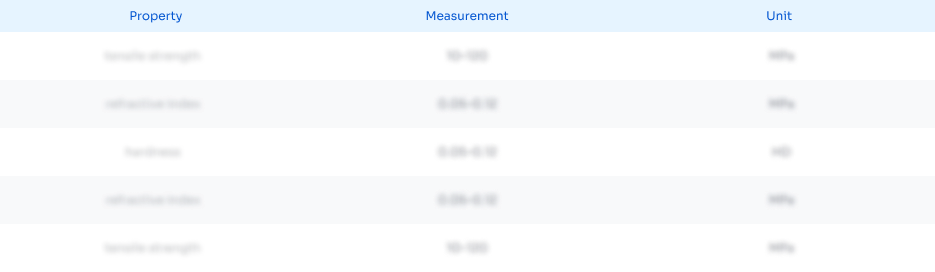
Abstract
Description
Claims
Application Information

- R&D
- Intellectual Property
- Life Sciences
- Materials
- Tech Scout
- Unparalleled Data Quality
- Higher Quality Content
- 60% Fewer Hallucinations
Browse by: Latest US Patents, China's latest patents, Technical Efficacy Thesaurus, Application Domain, Technology Topic, Popular Technical Reports.
© 2025 PatSnap. All rights reserved.Legal|Privacy policy|Modern Slavery Act Transparency Statement|Sitemap|About US| Contact US: help@patsnap.com