Process for rolling inner-corrugated combined surface metal composite tube
A metal composite pipe and joint surface technology, which is applied in the technical field of rolling inner corrugated joint surface metal composite pipe, can solve the problems of poor bonding performance of the composite interface, and achieve the effects of increasing the bonding strength, increasing the contact area, and simple process
- Summary
- Abstract
- Description
- Claims
- Application Information
AI Technical Summary
Problems solved by technology
Method used
Image
Examples
Embodiment
[0024] Embodiment: Preparation of stainless steel-carbon steel composite pipe
[0025] Billet making: Select 304 stainless steel pipe and Q345R carbon steel pipe to form billets according to the ratio of 1:3. The size of carbon steel pipe is 15mm thick×250mm diameter×2000mm long, which is used as cladding pipe 1; the size of stainless steel pipe is 5mm thick×248mm diameter×2000mm long. As the base pipe 2; clean the inner wall of the stainless steel pipe and the outer wall of the carbon steel pipe until the metal base is seen; stack the cladding pipe 1 and the base pipe 2, send them to the press for compaction, and use 10mm thick around the two ends of the stacked composite pipe blank The carbon steel is first spot welded and then packaged and welded by submerged arc welding. A hole is drilled at the end of the welded composite pipe blank to evacuate, and then the hole is closed to obtain a composite pipe blank, such as figure 1 , the thickness of the composite tube blank is 20...
PUM
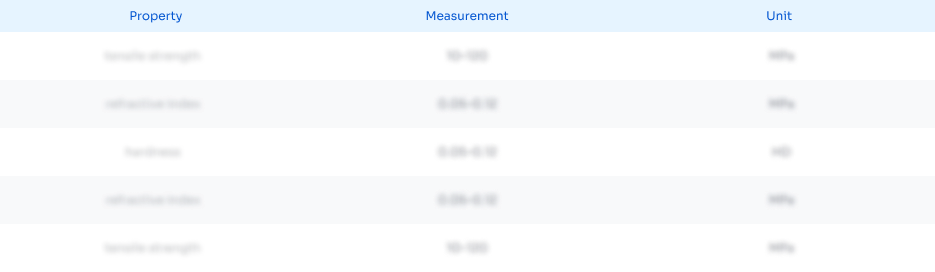
Abstract
Description
Claims
Application Information

- R&D
- Intellectual Property
- Life Sciences
- Materials
- Tech Scout
- Unparalleled Data Quality
- Higher Quality Content
- 60% Fewer Hallucinations
Browse by: Latest US Patents, China's latest patents, Technical Efficacy Thesaurus, Application Domain, Technology Topic, Popular Technical Reports.
© 2025 PatSnap. All rights reserved.Legal|Privacy policy|Modern Slavery Act Transparency Statement|Sitemap|About US| Contact US: help@patsnap.com