Flexible driving body and fast control mirror using the flexible driving body
A technology of rapid control and drive body, applied in the direction of optical components, optics, instruments, etc., can solve the problems of asymmetric structure, large mirror volume, inconsistent output, etc., to achieve increased resonance frequency, overall compact structure, long working life. Effect
- Summary
- Abstract
- Description
- Claims
- Application Information
AI Technical Summary
Problems solved by technology
Method used
Image
Examples
Embodiment Construction
[0028] The technical solutions of the present invention will be described in further detail below through specific implementation methods.
[0029] Such as Figure 1-3 As shown, a flexible driving body 4 includes a lens bearing horizontal plate 4-1, a rotation center rod 4-2, a first flexible leaf spring 4-31, a second flexible leaf spring 4-32, and a first input terminal for triangular amplification. Plate 4-41, second input end plate 4-42 of triangular amplification, threaded hole 4-5, threaded hole 4-6, first output end plate 4-71 of triangular amplification, second output end plate 4-72 of triangular amplification, Four identical triangular enlarged flexible rods 4-81~4-84, the first curved guide rod 4-91 and the second curved guide rod 4-92.
[0030] The first input end plate 4-41 of the triangular amplification, the second input end plate 4-42 of the triangular amplification, the first output end plate 4-71 of the triangular amplification, and the second output end plat...
PUM
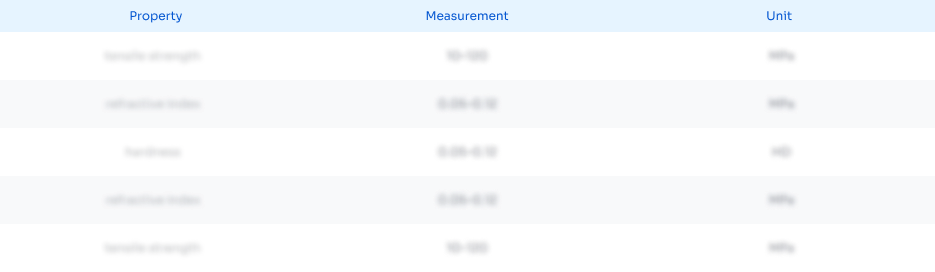
Abstract
Description
Claims
Application Information

- Generate Ideas
- Intellectual Property
- Life Sciences
- Materials
- Tech Scout
- Unparalleled Data Quality
- Higher Quality Content
- 60% Fewer Hallucinations
Browse by: Latest US Patents, China's latest patents, Technical Efficacy Thesaurus, Application Domain, Technology Topic, Popular Technical Reports.
© 2025 PatSnap. All rights reserved.Legal|Privacy policy|Modern Slavery Act Transparency Statement|Sitemap|About US| Contact US: help@patsnap.com