Roller surface flame spraying and clamping device and assembling method thereof
A technology of flame spraying and clamping device, which is applied in the direction of coating, molten spraying, metal material coating process, etc. It can solve the problems of cracks in the sprayed coating and deformation of the roller, etc., and achieve the elimination of uneven heat dissipation and discharge Flexible production and lower production costs
- Summary
- Abstract
- Description
- Claims
- Application Information
AI Technical Summary
Problems solved by technology
Method used
Image
Examples
Embodiment Construction
[0013] Referring to the accompanying drawings, the flame spraying clamping device on the surface of the roller includes a long axis 1, two flanges, an elastic member, an adjusting sleeve 6 and an adjusting nut 7. Both flanges are set on the long axis and are divided into fixed Flange 2 and movable flange 8, the fixed flange is fixed at one end of the long axis, the movable flange can move freely in the length direction of the long axis, the outer side of the movable flange is connected with one end of the adjustment sleeve through elastic parts connection, the other end of the adjustment sleeve is connected with the adjustment nut, and the adjustment nut is threaded with the long shaft.
[0014] The present invention is further improved, the movable flange is generally in the shape of a truncated cone, and its taper α is between 15-30°, 15° being the best, and the inner diameter of the roller to be clamped is between the diameter of the upper end surface and the lower end surfa...
PUM
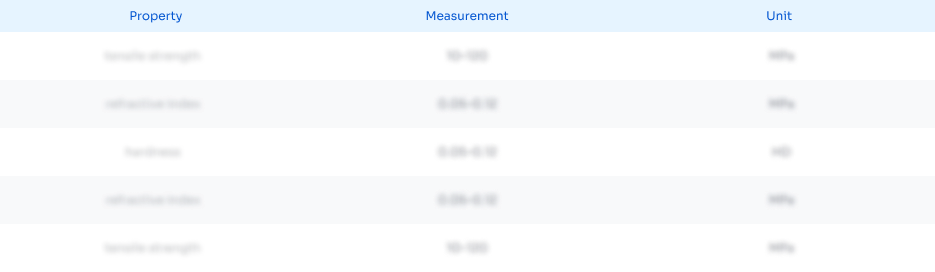
Abstract
Description
Claims
Application Information

- R&D
- Intellectual Property
- Life Sciences
- Materials
- Tech Scout
- Unparalleled Data Quality
- Higher Quality Content
- 60% Fewer Hallucinations
Browse by: Latest US Patents, China's latest patents, Technical Efficacy Thesaurus, Application Domain, Technology Topic, Popular Technical Reports.
© 2025 PatSnap. All rights reserved.Legal|Privacy policy|Modern Slavery Act Transparency Statement|Sitemap|About US| Contact US: help@patsnap.com