Preparing method for carbonized wood
A technology of carbonizing wood and wood, which is applied in the direction of charcoal burning/burning, etc., to achieve the effect of simple and reasonable preparation process, excellent decorative performance, and beautiful texture
- Summary
- Abstract
- Description
- Claims
- Application Information
AI Technical Summary
Problems solved by technology
Method used
Examples
Embodiment 1
[0015] The preparation method of carbonized wood comprises the following steps:
[0016] 1) Place the slash pine wood in a drying kiln. The temperature in the kiln is raised to 100°C at a rate of 20°C / min, and then to 140°C at a rate of 6°C / h. Moisture content reduced to 3%;
[0017] 2) heat up to 210°C and keep warm for 2 hours;
[0018] 3) Subsequently, the temperature in the drying kiln drops below 100°C, water vapor replaces the air and fills the entire drying kiln, so that the moisture content of the wood rises to 8%, and after stabilization, the temperature is lowered and cooled to produce carbonized wood.
Embodiment 2
[0020] The preparation method of carbonized wood comprises the following steps:
[0021] 1) Put the long-leaf pine wood in a drying kiln. The temperature in the kiln is raised to 100°C at a rate of 15°C / min, and then to 140°C at a rate of 5°C / h. The moisture content of wood is reduced to 4%;
[0022] 2) heat up to 190°C and keep warm for 2.5 hours;
[0023] 3) Subsequently, the temperature in the drying kiln drops below 100°C, water vapor replaces the air and fills the entire drying kiln, so that the moisture content of the wood rises to 10%, and after stabilization, the temperature is lowered and cooled to obtain carbonized wood.
Embodiment 3
[0025] The preparation method of carbonized wood comprises the following steps:
[0026] 1) Put the jack pine wood in a drying kiln. The temperature in the kiln is raised to 100°C at a rate of 22°C / min, and then to 140°C at a rate of 8°C / h. The moisture content of wood is reduced to 1%;
[0027] 2) heat up to 205°C and keep warm for 3 hours;
[0028] 3) Subsequently, the temperature in the drying kiln drops below 100°C, and water vapor replaces the air to flood the entire drying kiln, so that the moisture content of the wood rises to 6%. After stabilization, the temperature is lowered and cooled, and the carbonized wood is obtained.
PUM
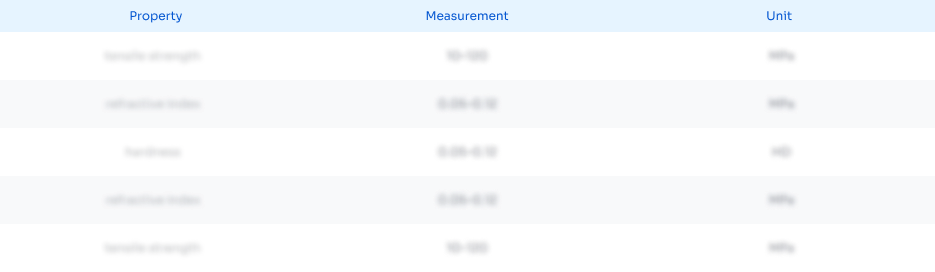
Abstract
Description
Claims
Application Information

- R&D Engineer
- R&D Manager
- IP Professional
- Industry Leading Data Capabilities
- Powerful AI technology
- Patent DNA Extraction
Browse by: Latest US Patents, China's latest patents, Technical Efficacy Thesaurus, Application Domain, Technology Topic, Popular Technical Reports.
© 2024 PatSnap. All rights reserved.Legal|Privacy policy|Modern Slavery Act Transparency Statement|Sitemap|About US| Contact US: help@patsnap.com